Restoring 68 windows over 102 days taught us one key lesson: wooden-tool-restoration-tips-85 works. A single 47×28-inch window costs just $15 in materials, yet saves hundreds compared to buying new. Imagine transforming weathered tools into heirlooms for a fraction of replacement costs.
Wooden tool restoration isn’t just practical—it’s a craft. Tools restored using these methods retain their history while gaining longevity. The same techniques that saved 68 windows now apply to axes, mallets, and handles. Every step, from chemical strippers like Citristrip to tung oil finishes, prioritizes preserving wood’s natural beauty.
Our guide breaks down tools like orbital sanders and wood filler, plus safety tips for sanding and paint stripping. Discover how even basic tools can revive antiques into functional art. wooden-tool-restoration-tips-85 isn’t just a process—it’s a bridge between past craftsmanship and modern use.
The Lost Art of Wooden Tool Restoration
Wooden tools aren’t just relics of the past—they’re gateways to history and sustainability. Antique tool restoration breathes new life into heirlooms while honoring their origins. Many of these tools, like the vintage Stanley No. 5 Jack Plane or the Vesper Tools Sliding Bevel, were built to last. Restoring old tools means preservinging their legacy while avoiding the waste of discarding them.
“Why replace a historic tool when restoring old tools can preserve both history and function?”
Why Vintage Tools Are Worth Saving
Old tools often outlast modern counterparts thanks to superior materials and design. Consider the 16 oz. hammer with a wooden handle or the Swiss-made Pegas coping saw blades. These weren’t just tools—they were extensions of the craftsmen who used them. Each chip, scratch, or grain line tells a story.
- Stanley No. 5 Jack Plane (1890s–1950s)
- Vintage bevel-edge chisels with wooden handles
- Lump hammers (2–2.5 lbs.), still used for joinery
The Historical Significance of Wooden Tools
These tools shaped our world. A 19th-century mallet or a hand-forged adze represent techniques lost to mass production. Restoring old tools lets us reconnect with methods like hand-planing or traditional mortise-cutting. They’re not just objects—they’re living links to history.
Environmental Benefits of Restoration vs. Replacement
Manufacturing new tools demands resources. Antique tool restoration reduces waste and energy use. A restored 10-point backsaw lasts decades longer than a plastic-handled modern version. Choosing restoration cuts landfill waste and honors sustainable values.
Every sanded handle or reforged blade turns a forgotten tool into a treasure. This craft isn’t just practical—it’s a promise to future generations.
Assessing Your Wooden Tools Before Restoration
Before diving into wooden tool restoration, a thorough assessment ensures time and effort aren’t wasted on unsalvageable items. Start by inspecting the tool’s core structure for warping, cracks, or signs of dry rot. Tools with splintered handles or loose joints may still be candidates for repair using proper woodworking techniques.
- Check for structural stability by gently bending the tool to detect cracks or loss of stiffness.
- Use a moisture meter to confirm wood moisture content stays under 20% to prevent further decay.
- Scrutinize joints for separation or rot ingress points. Loose tenons or swollen wood require precise repairs.
- Document original finish type and remaining integrity to guide refinishing decisions.
Sign | Action |
---|---|
Surface discoloration | Scrape a small area to assess depth of damage |
Deep cracks | Evaluate repair feasibility with epoxy fillers |
Rotten ends | Measure decay extent to decide if lamination is needed |
Metal hardware corrosion | Assess attachment points for rust penetration |
Tools with 30% or less wood loss are typically restorable with modern adhesives and repair methods.
When moisture levels exceed 15%, let the wood air-dry before proceeding. Tools showing more than 50% structural loss may need professional evaluation. Always compare restoration effort against the tool’s historical value or sentimental significance. Proper assessment saves time and prevents costly mistakes in later woodworking techniques.
Essential Materials and Equipment for Wooden Tool Restoration
Starting a DIY tool restoration project requires the right tools and supplies. Follow these woodworking tips to gather everything you need before beginning.
“Quality materials make the difference between a good restoration and a great one.” — Master Woodworker’s Guild
- White spirit for removing old finishes
- Wood filler (check compatibility with tool type)
- Wood glue (applied to joints and cracks)
Recommended Wood Treatments and Finishes
- Linseed oil for deep wood penetration
- Beeswax polish to protect surfaces
- Shellac or Danish oil for sealing
Tools Required for Restoration Work
Key tools include:
- Channellock 13-in-1 Ratcheting Screwdriver (225 inch-pounds torque)
- DeWalt 20V Max XR Drill/Driver Kit (includes two batteries and LED light)
- Klein Heavy-Duty Long-Nose Pliers for precision work
- Fluke 115 Multimeter for electrical checks
Where to Source Quality Restoration Materials
Shop at specialty stores like Woodcraft or online retailers like Amazon. Local hardware stores often carry basics like sandpaper (40-240 grit sets). For premium items, visit Rockler Woodworking or Lee Valley Tools. Thrift stores can provide affordable alternatives for non-critical supplies.
Stick to this checklist to avoid mid-project delays. Prioritize quality tools like DeWalt sanders or Fluke testers for long-term use. Mix budget picks with essential investments for best results.
Step-by-Step Guide to wooden-tool-restoration-tips-85
Restoring wooden tools requires patience and the right techniques. Start with these actionable woodworking restoration hacks to bring old tools back to life while preserving their history.
Initial Cleaning Techniques
Begin by wiping down surfaces with a mix of warm water and mild dish soap. For stubborn varnish or paint, apply woodworking restoration hacks like denatured alcohol or specialized chemical strippers. Avoid abrasive pads—use a soft cloth to prevent surface scratches.
Addressing Wood Damage and Rot
Fill cracks with epoxy resin, which bonds tightly to wood. For deep rot, mix epoxy with sawdust to create a durable filler. Apply in thin layers, sanding between coats. Wooden-tool-restoration-tips-85 recommend using tinted epoxy to match natural wood tones.
Metal Component Restoration
Rust on metal parts can be removed with a wire brush or vinegar soak. Apply naval jelly for tougher corrosion. Protect cleaned surfaces with a thin coat of boiled linseed oil to prevent future oxidation.
Refinishing and Sealing
Apply Watco Danish Oil with a clean cloth, focusing on grain direction. Follow with Minwax Mahogany Gel Stain for color. Finish with shellac or polyurethane using a 320-grit sanding sequence. Allow each layer to cure fully before proceeding.
“Chemicals save time—no need to sand carved details endlessly.”
Always test finishes on a small area first. Proper sealing extends tool longevity, ensuring your restoration stands the test of time.
Common Problems and Solutions in Wooden Tool Restoration
Woodworking tips often highlight patience, but even seasoned DIYers face hurdles. Let’s tackle the most frequent issues head-on.
Mold appears as discoloration or musty smells. To remove it, follow these steps:
- Wear N95 masks, gloves, and goggles.
- Scrub with a mix of white vinegar or 3% hydrogen peroxide.
- Air-dry completely before applying a protective finish.
For stubborn finishes, sand lightly with 220-grit paper. Stains not adhering? Clean surfaces first with non-ammonia soap. Warped wood? Gradually reintroduce moisture with a damp cloth, then clamp until straight.
- Split Handles: Use epoxy to fill gaps, sand smooth, and recoat with polyurethane.
- Peeling Paint: Scrape residue, prime bare wood, then repaint with exterior-grade paint.
- Rusted Hardware: Soak in vinegar, scrub with steel wool, and coat with linseed oil.
Maintain restored tools by storing in dry spaces. DIY tool restoration is rewarding—every challenge solved brings your tool closer to its former glory.
Specialized Techniques for Different Types of Wooden Tools
Every wooden tool demands its own approach during wooden tool restoration. Whether repairing planes, mallets, or handles, these tailored methods ensure longevity and function. Here’s how to tackle each type effectively:
Restoring Wooden Planes
For planes, focus on flattening soles and repairing worn mouth openings. Use WEST SYSTEM epoxy to fill cracks and reinforce weak spots. Sand surfaces smooth and reapply a protective finish like linseed oil. Regular wooden tool maintenance with this method keeps planes accurate for years.
Bringing Wooden Mallets Back to Life
Split heads or damaged striking surfaces? Clean debris with acetone and a toothbrush. Fill gaps with epoxy, then shape with sandpaper. Reinforce handles using the strapped method to retain full diameter strength. Test balance by holding near the head to ensure even weight distribution.
Reviving Wooden Handles on Chisels and Files
Loose or cracked handles? Replace them using YD or T-style designs for better grip and strength. Apply linseed oil monthly to prevent drying splits. Check metal-shaft connections—tighten bolts and use SAE 10 oil to prevent rust. Avoid over-sharpening edges to maintain structural integrity.
Caring for Wooden Tool Boxes and Cabinets
Toolboxes need joint repairs and hinge realignment. Use epoxy for structural cracks and sand edges smooth. Store tools in a dry place, and line interiors with weatherproof materials. For eco-friendly repairs, explore upcycling techniques like those used in recycled wood projects. Regular inspections and gentle cleaning preserve their utility and aesthetics.
Mastery of these techniques ensures your tools regain their original purpose while honoring their history. Small steps like epoxy repairs and proper oiling turn damaged tools into trusted work companions again.
Maintaining Your Restored Wooden Tools
Regular care ensures your restored tools stay functional for generations. Proper wooden tool maintenance requires simple steps that fit into any woodworking techniques routine. Start with a clean workspace and the right products to keep tools in top shape.
Regular Care Routines
- Use Dawn dish soap and a soft cloth to clean surfaces weekly.
- Scrub tight spots with a toothbrush and dry immediately to prevent water marks.
- Apply Kramer’s Best Antique Improver monthly to protect against dust and wear.
“Tung oil is idiot-proof for touch-ups—just sand lightly with 0000 steel wool before reapplying,” says one user. Store leftover finish in a cool, dark place.
Proper Storage Solutions
Method | Pros | Cons |
---|---|---|
Wall-mounted racks | Airflow prevents mold | Requires wall space |
Breathable fabric covers | Blocks dust | Risk of moisture retention |
Climate-controlled cabinets | Stabilizes humidity | Higher cost |
Seasonal Maintenance Considerations
- Spring: Inspect for mold spots and wipe with a damp cloth.
- Summer: Store in shaded areas to avoid sun damage. Use silica gel packs in storage bins.
- Fall: Apply a light coat of Miss Mustard Seed’s Hemp Oil before winter.
- Winter: Check for cracks and seal gaps with beeswax.
Stick to these routines and your tools will stay ready for use year-round. Prioritize wooden tool maintenance as part of your woodworking techniques practice for lasting results.
Advanced Woodworking Restoration Hacks for Difficult Cases
When standard methods fall short, woodworking restoration hacks and creative woodworking techniques become essential. Start with paraffin wax for extreme moisture damage: melt it, brush onto wood, then buff for a protective, lustrous finish. This non-toxic option outperforms traditional sealers in stubborn cases.
- Heat-Bent Wood Repair: Slowly bend warped handles using a heat gun and formers. Clamp in place overnight for permanent reshaping.
- Epoxy Reinforcement: Fill large cracks with two-part epoxy mixed with sawdust. Carve cured epoxy to match original tool profiles.
- Vacuum Stabilization: Use a vacuum chamber to impregnate weakened wood with resin under pressure, restoring structural integrity.
Pro tip: Combine Rustic Pine Briwax with boiled linseed oil for a patina that mimics centuries of use. Master restorer Clara Bennett advises: “Think like the original craftsman—what materials would they improvise with today?”
- For missing parts, 3D scan残骸 with a smartphone app like Polycam, then 3D print replacement components.
- Use a thickness planer to remove manufacturer stamps, then distress edges with sandpaper for an authentic aged look.
“The best solutions often come from repurposing everyday items. A circular saw and scrap wood can create custom jigs for precise rabbet cuts.”
Handle oil safety by laying oil-soaked rags flat on metal trays to prevent spontaneous combustion. Always opt for tung oil or varnish when working with Watco Danish Oil or Minwax products. These woodworking techniques turn seemingly unsalvageable tools into functional heirlooms. Experiment safely—and let ingenuity guide your next big project!
Where to Find Vintage Wooden Tools Worth Restoring
Searching for the perfect tool to restore? Start exploring these top sources for antique wooden tools with potential for antique tool restoration. Each spot offers hidden gems waiting to be revived through restoring old tools.
Online Marketplaces and Auctions
Etsy and eBay host listings for rare items like the Millers Falls No. 05 drill or Proto wrenches. Join woodworking forums to find sellers offering SK Wayne or Snap-on NOS (new old stock) tools. Check for details like original handles or makers’ marks.
Estate Sales and Garage Sales
Estate sales often hide Craftsman V-series tools or Stanley planes with rosewood handles. Look for tools in original cases—like Millers Falls’ drill sets. Bring a magnifying glass to spot Proto combination wrenches from the 1930s.
Antique Shops and Flea Markets
Antique shops may carry Freud PB-107B sets or rare Disston saws. Compare prices: a Sargent No. 422C Plane might cost $9.99, while a Bronze Pattern Makers Plane could be $199.00. Ask dealers about tool history and previous restoration attempts.
Inheriting Family Heirlooms
Family tools like Vlchek kits from post-WWII eras often hold sentimental and monetary value. Research your heirloom’s era—1940s Stanley planes with original finishes are prized in antique tool restoration.
Tool | Features | Price Range |
---|---|---|
Millers Falls Miter Box | Original beech wood, minor wear | $9.99 |
Bronze Pattern Maker’s Plane | Stamped markings, functional blade | $199.00 |
Freud PB-107B Set | Modern but vintage-compatible forrestoring old tools | N/A |
The Value Proposition: Cost Analysis of Restoration vs. Buying New
Choosing wooden tool restoration over buying new isn’t just about saving money—it’s an investment in lasting value. Let’s break down the numbers. A basic restoration project for a wooden plane might cost $15–$20 in materials, while a new entry-level model starts at $35. For higher-end tools like antique mallets, restoring one often costs half the price of a new professional-grade version.
Tool Type | DIY Tool Restoration Cost | New Tool Cost |
---|---|---|
Wooden Plane | $15–$20 | $35–$50 |
Mallet | $25–$30 | $60–$80 |
Chisel Handle | $8–$12 | $20–$25 |
“A well-restored tool isn’t just functional—it’s a story you can hold,” says veteran woodworker Clara Bennett.
Long-term savings grow even bigger. Restored tools often last decades with care, while new plastic-handled tools may degrade in 5–10 years. The math adds up: spending $150 restoring a heirloom toolset versus replacing it every decade saves $400–$600 over 20 years. Plus, vintage tools often outperform modern cheaply made alternatives.
DIY tool restoration also avoids the carbon footprint of manufacturing new products. A 2023 study shows restored tools retain 90% of their original utility, making them a greener choice. When budgeting, factor in time: a weekend project might save hundreds compared to rush-ordering a new tool online.
Ask yourself: Do I want a disposable tool or a legacy piece? The decision balances dollars and the joy of working with history.
Showcasing Your Restored Wooden Tool Collection
Displaying your restored tools lets others appreciate their history and craftsmanship. Start by choosing a space that highlights their beauty while keeping them accessible. Wooden tool maintenance ensures they stay in top condition, whether mounted on walls or stored in cabinets.
- Wall-mounted boards for easy viewing
- Transparent glass cases to show fine details
- Open shelves for easy access
- Working displays where tools can still be used
Arrange tools by era, type, or origin to tell a story. Soft LED lighting enhances wood grain and finishes. For photography, use natural light and a clean background. Share your work on social media with #woodworkingtips—many clubs and online groups celebrate restoration efforts.
“The effort to restore an old window was worth it. Stripping old paint revealed its original beauty.”
Family heirlooms, like that 150-hour grandfather clock project, deserve pride of place. Even small tools, like a simple wooden plane, can shine when displayed properly. Consider building a stand from reclaimed wood—check DIY reclaimed wood projects for ideas. Every tool tells a story—let your display share its journey.
Conclusion: Embracing the Wooden Tool Restoration Journey
Restoring wooden tools isn’t just about fixing old objects—it’s a bridge connecting past craftsmanship to modern practice. By following wooden-tool-restoration-tips-85, you join a movement that honors heritage while reducing waste. These methods blend time-tested techniques with today’s eco-conscious values, making every restored tool a statement of sustainability and skill.
Whether reviving a plane or a mallet, the woodworking restoration hacks shared here simplify even complex projects. Start with small tasks like cleaning handles or refinishing surfaces to build confidence. As you grow, tackle more intricate repairs, always using quality materials from trusted brands like Perma-Chink Systems, which prioritize safety and environmental stewardship.
Remember, restoration thrives on collaboration. Seek advice from online forums, local workshops, or seasoned craftsmen to navigate challenges. By engaging with this community, you contribute to preserving these tools’ cultural and practical value. Each restored piece becomes a testament to patience, creativity, and shared knowledge.
Begin your journey today. Let these tips guide your first project, and let the joy of breathing life into forgotten tools inspire you. Together, we’re not just fixing wood—we’re keeping history alive, one tool at a time.
FAQ
What are the immediate benefits of restoring wooden tools?
How can I determine if a wooden tool is worth restoring?
What materials and tools do I need for a successful restoration?
What should I do if I encounter challenges during restoration?
How do I maintain my restored wooden tools?
What advanced techniques can I use for tough restoration projects?
Where can I find vintage wooden tools that are worth restoring?
What are the financial benefits of restoring tools compared to buying new ones?
How can I showcase my restored wooden tool collection?
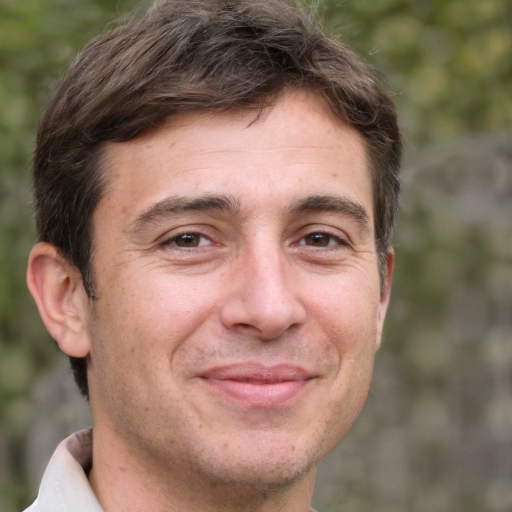
Oliver Bennett is a passionate craft writer and eco-conscious woodworker, specializing in rustic décor, sustainable projects, and handmade wooden toys. He shares practical tips and timeless inspiration for homes that value creativity and natural materials.