Did you know that the global market for wooden wall art could hit $9.2 billion by 2027? This surge highlights a growing appreciation for tactile artistry, including the intricate craft of wooden-architectural-miniatures-tips-97. While digital models dominate modern design, physical miniatures remain unmatched in their ability to convey scale and texture. These tiny structures let architects and hobbyists explore ideas through touch, offering a three-dimensional blueprint that even the largest screens can’t replicate.
From ancient Greek temples to modern skyscrapers, miniatures have always been a bridge between imagination and reality. Today’s enthusiasts use time-tested methods like hand-carving and precise joinery—techniques detailed in resources like architectural model making tips—to craft models that feel both historic and modern. Whether for professional presentations or personal passion projects, mastering these skills turns raw wood into stories that any architect or DIYer can proudly display.
Understanding the Art of Wooden Architectural Miniatures
Wooden architectural models have captivated creators for centuries, blending history with modern creativity. These miniature wooden structures are more than decorative items—they are bridges between imagination and reality.
The Historical Significance of Architectural Models
Early civilizations used scaled-down versions of buildings to plan and present designs. By the Renaissance, architects like John Thorp refined techniques, creating detailed wooden replicas. Even as materials choices evolved—Builder journal noted cardboard models in the 19th century—wood remained a staple. A model of the Pantheon, crafted in wood, exemplifies this tradition. These models became both tools and artifacts, preserving architectural evolution.
Architectural models were made using pasteboard and cardboard, as noted in the Builder journal in 1862 and 1906.
Why Wooden Miniatures Continue to Captivate Enthusiasts
Today, wooden architectural models retain their allure. Their tactile nature offers warmth digital tools can’t replicate. Wood’s texture and natural imperfections add authenticity. Techniques like dry-brushing mimic weathering, enhancing realism. Enthusiasts often cite the 4D Modelshop as a hub for materials and inspiration, proving these creations remain a vibrant craft.
- Wood’s organic feel connects creators to their craft.
- Miniature wooden structures become heirlooms, preserving design ideas physically.
The Therapeutic Benefits of Creating Miniature Structures
Crafting miniature wooden structures offers more than aesthetic rewards. The meticulous work—measuring, sanding, assembling—becomes a meditative practice. Each detail, like carving window frames, requires focus that silences stress. Completing a model delivers tangible pride, fostering mental well-being. For many, this hands-on artistry is both a hobby and a mental health tool.
- Focus on precision reduces distractions.
- Seeing progress boosts confidence.
Essential Tools for Crafting Wooden Architectural Miniatures: Tips-97
Every project starts with the right tools. Whether you’re a beginner or an expert, quality wooden model making supplies ensure your miniatures look professional. A sharp scalpel and precise ruler make all the difference when shaping tiny details. Here’s what belongs in your toolkit:
- Scale Ruler: A triangular 3-sided ruler with paired scales (like 1:1250 and 1:2500) keeps measurements clear.
- Mechanical Pencil: 0.3mm H lead draws fine lines for templates and plans.
- Scalpel: Swann-Morton No.3 handles with 10A blades cut smoothly through Palight foamed PVC and Obeche wood.
- Cutting Mat: A2 size with a cm grid protects work surfaces while guiding precise cuts.
- Metal Ruler: A 60cm steel ruler with masking tape backing prevents slipping during delicate work.
- Try Square: An engineer’s version ensures perfect 90-degree angles for walls and corners.
“The right tools turn visions into tangible masterpieces.” – Professional Model Maker
Invest in tools that handle micro-scale precision. A quality scalpel or fine chisels let you carve intricate details, while a clean cutting mat avoids surface damage. For joining pieces, use PVA glue for seamless bonds. Remember, even small tools like a 0.3mm pencil or a tiny try square multiply accuracy. When building wooden-architectural-miniatures-tips-97, every tool matters. Start with these essentials and watch your designs come to life with precision.
Selecting the Right Woods for Your Miniature Projects
Choosing the perfect wood is the first step in creating durable and detailed miniature structures. The right miniature building materials ensure your models last while showcasing intricate designs. Let’s explore how wood type impacts every stage of your project.
Hardwoods vs. Softwoods: Making the Right Choice
Type | Best Uses | Key Traits |
---|---|---|
Hardwoods (e.g., basswood, cherry) | Structural elements, detailed carvings | Strong, fine grain, resists warping |
Softwoods (e.g., pine, balsa) | Frames, lightweight components | Easily cut, cost-effective |
Hardwoods like basswood are ideal for wooden miniature building techniques requiring precision. Their dense grain holds delicate details but needs gentle, steady cuts to avoid splitting. Softwoods, though lighter, may require reinforcement for heavy features. Always work with the grain direction to prevent cracks.
Specialty Woods for Detailed Architectural Features
- Boxwood: Perfect for tiny carvings like window moldings.
- Pearwood: Smooth texture for smooth curves in columns or banisters.
- Holly: Uniform grain makes it great for inlays and paneling.
Sustainable Wood Options for Eco-Conscious Crafters
Opt for eco-friendly choices without sacrificing quality. Try:
- Reclaimed wood scraps from local suppliers.
- FSC-certified exotic woods like mahogany.
- Bamboo for lightweight, renewable alternatives.
Even small wood pieces can add character—think tiny shingles from leftover planks!
Precision Cutting Techniques for Miniature Wooden Components
Perfect cuts transform miniature models into lifelike structures. Use sharp blades and steady hands to achieve flawless angles and curves. These architectural model makinging tips simplify cutting even the smallest details without damaging delicate materials.
Material | Optimal Use |
---|---|
Palight Foamed PVC | Clean miter joints and flat surfaces |
Stencil Card | Thin, bendable parts like window sashes |
Mastering Miter Cuts for Perfect Corners
For sharp angles:
- Use a miniature miter box with adjustable slots
- Mark lines with a fine-tip marker for visibility
- Test cuts on scrap material before final pieces
Creating Curved Elements with Confidence
Curved edges demand patience. Start by sketching shapes lightly.
- Use a scalpel for intricate arcs
- Score lines gently before full cuts
- Sand curves after cutting to smooth edges
Troubleshooting Common Cutting Challenges
Issue | Solution |
---|---|
Blade slipping | Use a cutting mat for grip |
Split wood fibers | Cut slowly in multiple passes |
Always check blade sharpness before starting. Dull blades cause jagged edges. For architectural model construction, precision beats speed. Store tools properly to keep blades in top condition.
Joining Methods for Delicate Wooden Architectural Models
Joining components in wooden scale models demands ingenuity to maintain strength without overwhelming tiny details. Traditional carpentry methods scale down into clever alternatives that prioritize both stability and precision. These wooden miniature building techniques transform fragile pieces into cohesive structures through smart material choices and adhesive tricks.
“A well-made joint should look like it belongs there, not like it was forced,” advises modelers guild standards.
- Butt joints reinforced with super glue or hide glue create sturdy connections between small parts.
- Lap joints simplify by overlapping thin wood layers glued at edges, avoiding complex interlocking.
- Miniature dowels made from toothpicks or wire pins mimic full-scale joints in a compact form.
- Mitered corners gain strength from tiny brads or precise glue application, hiding gaps with sanding.
- Visual tricks like carved grooves simulate dovetails, giving the illusion of traditional joinery.
Palight foamed PVC cuts cleanly into decorative trims or base layers, then bonded with wood using PVA glue. Layering stencil card under wood adds thickness without bulk, a trick from pro modelers toolboxes. Temporary holds with wax or tape keep pieces aligned during drying.
Reinforcement methods like gussets or cross-bracing add hidden support, while wire brads secure curved elements. These methods ensure joints match the model’s scale, whether recreating a Victorian townhouse or a modernist structure. Every connection becomes part of the design story.
Adding Authentic Details to Your Miniature Wooden Structures
Enhance miniature architecture designs by mastering details that transform wooden architectural models into lifelike masterpieces. Every element—from windows to weathering—adds depth that captivates viewers.
Crafting Realistic Windows and Doors
Start with precision-cut window frames using 0.8mm obeche wood glued directly to paper templates with PVA adhesive. This technique locks designs in place, ideal for unseen back surfaces. For doors, attach hinges with tiny screws or bent wire for a functional look. Pro tip: Use a scalpel to carve delicate window mullions for Gothic-style models.
- Thin wood strips simulate stained glass patterns when layered over translucent film
- Apply gold leaf to door handles for ornate finishes
Creating Miniature Roof Shingles and Tiles
Roof Type | Material | Application |
---|---|---|
Shingles | Thin cedar slices | Layer at 45° angles using PVA glue |
Clay Tiles | Carved basswood | Score with a knife to create overlapping patterns |
Techniques for Simulating Weathered Wood
Age wooden architectural models naturally using these methods:
- Apply diluted coffee stains for sun-bleached effects
- Sand edges of wood to mimic erosion
- Use sandpaper to distress painted surfaces
Incorporating Landscape Elements
Complete scenes with:
- Miniature trees made from twisted wire and green flocking
- Gravel paths glued with matte medium
- Water features using glossy resin for reflective surfaces
For advanced details, Wonderhood Corner Shops sets provide pre-cut structures to populate model villages. KEVA planks work wonders for building fences and garden edging.
Finishing Techniques to Elevate Your Wooden Scale Models
Finishing isn’t just about protection—it’s the final step to bring wooden scale models to life. Start by sanding surfaces with 220-grit paper to smooth edges without blurring details. For a natural wood look, apply OsmoColor Dekorwachs, a wax-oil blend that enhances grain without adding bulk. When replicating aged patinas, mix acrylic paints to mimic weathered wood or metallic oxidation.
- Use RustOleum Clear Sealer for a water-resistant coat that stays clear on delicate surfaces.
- Simulate stone textures by printing marble patterns on inkjet transparency film (OHP) and transferring them to PVC, sealed with acetate.
- Add depth with dry-brushing: load a fine brush with pigment, wipe excess, and drag along edges for subtle highlights.
For metallic finishes, apply Humbrol enamels as base coats before adding metallic powders for a believable sheen. When working with 0.6mm veneers from brands like Vale Veneers, secure edges with superglue then smooth with sandpaper. Avoid over-saturating wood with finishes; thin layers prevent warping in small-scale models.
Protect finishes with UV-resistant coatings to prevent fading. Explore layering stains and paints for aged looks—check techniques for color washing to achieve subtle graying on rooftops or walls. Test finishes on scrap wood first to ensure they don’t obscure intricate details.
Remember, the goal is realism: a tiny column’s fluted details need as much care as a full-sized counterpart. Patience with these wooden-architectural-miniatures-tips-97 ensures your model’s finishes tell a story of authenticity at any scale.
Scaling and Proportions: The Mathematical Side of Architectural Model Construction
Getting scale right is the secret to making miniature wooden structures feel lifelike. Whether building a 1:50 cottage or a 1:25 skyscraper, math ensures every detail lines up perfectly. Here’s how to master the numbers behind the craft.
Common Scale Ratios for Architectural Miniatures
Choose scales that balance detail and size. Popular ratios include:
- 1:2 (half-size, for close-up study models)
- 1:25 (ideal for small rooms or furniture)
- 1:50 (standard for urban layouts)
- 1:100 (cityscapes and large buildings)
Use this formula to adjust sizes: (desired size / real size) Ă— 100 = percentage to scale. For example, scaling a 10m wall to 1:100 becomes 10cm in your model.
Tools for Accurate Measurements
Triangular scale rulers shine for precision. Their bold markings and multiple edges (like 1:20 and 1:50 on different sides) cut guesswork. Opt for rulers with 2cm divisions for sharp details. Pair these with proportional dividers for spacing accuracy. Digital apps like ScaleCalc or SketchUp automate tricky calculations.
Translating Plans into Miniature Reality
Start by tracing blueprints onto grid paper, then apply your chosen scale. Simplify complex features—like merging small window panes into single pieces. Remember: tiny elements like door handles may need slight enlargement to stay visible. Always double-check measurements using your scale ruler’s edges.
Preserving and Displaying Your Miniature Architecture Designs
Protecting your miniature creations starts with understanding their environment. Wooden miniatures react to humidity and temperature shifts, warping or cracking over time. Miniature building materials like wood need stable conditions—ideally 45-55% humidity and 68-72°F. Avoid placing models near windows or heating vents to prevent fading and distortion.
Climate Considerations for Wooden Miniatures
Rob Hawkins, a seasoned miniature artist, emphasizes sealing wood with spray primers like Simoniz acrylic to lock in moisture resistance. For outdoor-inspired scenes, Kapa-line foamboard and styrofoam treated with Mod Podge create durable bases that resist humidity. Test small samples first to ensure materials like resin or foam hold up over time.
Custom Display Case Options
- Opt for acrylic or glass-fronted cases with breathable padding to block dust.
- DIY cases can use modular foamboard sections for easy access without disassembling your design.
- Incorporate LED strips inside cases to highlight textures without heat damage.
“Modular construction lets you transport miniature architecture designs safely. Break scenes into sections using foamboard platforms—this protects delicate parts during travel.”
Lighting Techniques to Showcase Your Work
LED lighting adds drama without risking heat warping. Undercase LED strips highlight baseboards, while tiny bulbs inside structures mimic indoor lighting. For water features, resin-coated LEDs create realistic reflections. Always test lighting angles to avoid harsh shadows on fine details.
Pro tip: Store models in acid-free boxes with silica gel packets when not displayed. Use velvet or felt padding to secure miniature building materials like foam or wood during transit. Proper preservation ensures your creations stay vibrant for years.
Conclusion: Embracing the Craft of Wooden Architectural Miniatures
Wooden miniature building techniques bridge centuries of tradition with modern creativity. Whether recreating historic buildings or designing futuristic structures, the skills shared here empower makers to craft models that resonate as both art and functional design. Architectural model making tips covered—from precision cutting to weathered finishes—highlight how even small details amplify a model’s storytelling power. These methods ensure your creations feel authentic, inviting viewers to imagine the full-scale architecture they represent.
Today’s demand for architectural models remains strong, with firms like 4D modelshop and Network Modelmakers proving their enduring value. While digital tools dominate, physical models offer irreplaceable tactile insights. The Japanese approach, blending sugi wood traditions with modern projects like Tokyo SkyTree, shows how cultural heritage can inspire sustainable practices. By choosing eco-friendly woods and respecting materials, makers honor both craftsmanship and the planet.
Begin your journey with accessible tools and materials. Platforms like Etsy and Miniatura connect hobbyists to resources, while online tutorials demystify techniques. Remember, mastery grows through trial and error. Each cut, join, and finish deepens your connection to architecture’s history and your own creativity. Whether for personal joy or professional presentation, wooden miniatures transform abstract designs into tangible stories. Embrace this craft to explore the beauty of scale, texture, and the quiet satisfaction of hands-on creation.
FAQ
What are the best tools for crafting wooden architectural miniatures?
Which woods are recommended for architectural miniature projects?
How do I make precise cuts for miniature wooden components?
What joining methods work best for delicate miniature models?
How can I add authentic architectural details to my wooden structures?
What finishing techniques can enhance the appearance of wooden miniatures?
How do I maintain accurate scale and proportions in my designs?
What should I consider when displaying wooden architectural miniatures?
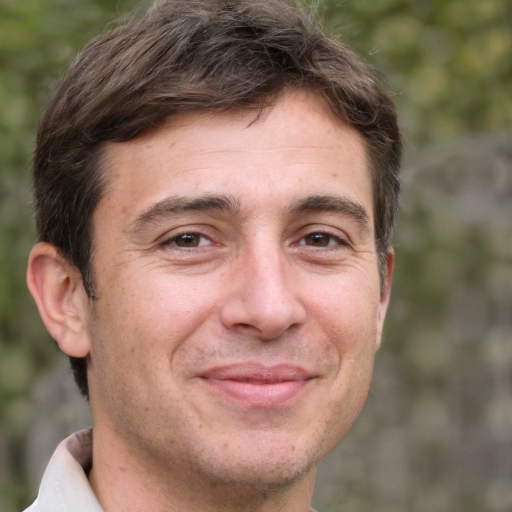
Oliver Bennett is a passionate craft writer and eco-conscious woodworker, specializing in rustic décor, sustainable projects, and handmade wooden toys. He shares practical tips and timeless inspiration for homes that value creativity and natural materials.