Did you know that a single Japanese Ryoba saw can stay razor-sharp for decades with proper care? This 300mm pull saw isn’t just a tool—it’s a bridge connecting modern woodworkers to centuries of traditional woodworking techniques. traditional-joinery-without-power-tools-tips-41 unlocks the secrets to creating furniture that lasts generations, using methods proven since ancient Egyptian joinery.
From mortise chisels to layout squares, traditional woodworking techniques rely on hand tools that demand precision over power. These methods aren’t just nostalgic—they’re a proven way to craft joints so strong they’ve withstood wars, earthquakes, and time. Whether building a table or a chair, the skills in this guide let you master dovetails with a Dozuki saw or carve smooth curves with a coping saw, all without a single motorized tool.
Discover how tools like the Japanese water stone or a wooden mallet transform raw wood into heirloom-quality pieces. This article reveals step-by-step strategies to build joints that modern power tools often overlook. You’ll learn why a block plane beats electric sanders for end-grain smoothing and how a simple marking knife ensures flawless layouts every time. traditional-joinery-without-power-tools-tips-41 isn’t just about avoiding electricity—it’s about mastering craftsmanship at its purest form.
The Rich Heritage of Hand Tool Joinery
Traditional wood joinery tutorials reveal timeless skills passed through generations. These handcrafted joinery methods forged the foundations of furniture making, blending artistry with functional strength. From colonial-era chests to heirloom-quality tables, these techniques endure because they work.
How Traditional Joinery Shaped Woodworking History
Centuries of trial and error refined joints like dovetails and mortise-and-tenon. A 14-joint tool chest built entirely by hand proves their structural reliability. Historical records show 18th-century craftsmen used these methods to create furniture that survives today, demonstrating their lasting value.
Why Modern Woodworkers Are Returning to Hand Tools
- Efficiency: Students built 30+ projects in 24 days using only hand tools
- Artistic connection: 20-30 minute dovetails require precision over speed
- Inspired by pioneers like Tom, who revived interest in techniques documented in Robert D. Mussey’s works
The Sustainability Benefits of Traditional Joinery
Handcrafted joinery methods reduce environmental impact significantly:
Traditional | Modern |
---|---|
No electricity required | Dependent on power tools |
90% material utilization | Higher waste rates |
Repairable joints last decades | Disposable furniture trends |
Narex mortising chisels exemplify how modern artisans blend old-world precision with contemporary tool quality. This synergy keeps traditional practices alive while addressing today’s eco-conscious markets.
Essential Hand Tools for Traditional Joinery Work
Mastering hand tool woodworking tips starts with the right equipment. These tools form the backbone of woodworking without power tools, enabling precision and control in every joint. Begin with a core set and expand gradually as skills grow.
- Saws: A 26-30 inch Western-style rip saw (5 TPI) and crosscut saw (8 TPI) handle basic cuts. Add a 14-22 TPI back saw for dovetails and a 15 TPI coping saw for intricate shaping.
- Planes: A #4 smoothing plane for surface prep, a #5 jack plane for stock reduction, and a #8 try plane for long boards. Add a block plane for end grain trimming.
- Chisels: A 1/8″–1″ bevel-edge set from brands like Narex. Include a dedicated mortise chisel for deep cuts and a paring chisel for fine work.
- Marking Tools: A layout square, marking knife, and two-pin marking gauge ensure accurate lines. A combination square checks squareness, while dividers transfer measurements.
- Maintenance Gear: Sharpening stones (1000-6000 grit), strops, and a wooden mallet for striking chisels. Files (triangular and rat-tail) refine edges and curves.
- Clamping Systems: Start with a few quick-release bar clamps. Add pipe clamps for large projects and wooden hand clamps for delicate work.
Quality matters more than quantity. Invest in a Japanese pull saw first, then build around it. Sharpening stones and a set of 1/8″, 1/4″, and 3/8″ chisels form a starter kit. Avoid cheap steel—look for tools with hardened blades like Narex or Lie-Ni. Regular honing keeps edges razor-sharp for clean cuts.
Begin with core tools and add specialized items as projects grow. This setup turns any workshop into a hub for timeless joinery craftsmanship.
Understanding Wood Behavior for Successful Traditional-Joinery-Without-Power-Tools-Tips-41
Mastering wood behavior is key to traditional-joinery-without-power-tools-tips-41. Wood’s natural tendencies affect joint longevity. Let’s explore how to work with—not against—its nature.
Reading Grain Direction for Optimal Joint Strength
Grain direction dictates joint durability. Always align wood grain so it flows naturally into joints. Cross-grain joints risk splitting. Use a marking gauge like the reliable Marples gauge to map grain patterns. Softwoods like pine may require wider joints to compensate for weaker fibers.
Selecting the Right Wood Species for Your Joints
- Hardwoods such as oak and maple offer stability for mortise-and-tenon joints.
- Softwoods like spruce are ideal for lightweight projects but need extra care in alignment.
- Exotic woods like teak resist moisture but demand precise cuts with tools like Bailey planes.
Accounting for Seasonal Wood Movement
Wood expands and contracts with humidity. A 12-inch board can swell up to 3/16″ in rainy seasons. Design joints to accommodate this shift. Use loose-fitting dovetails or sliding dovetails in drawer sides. Traditional artisanal joinery practices often employ mortise-and-tenon joints with clearance slots to allow movement without compromising structure.
Always pre-dry wood to 6-8% moisture content. Use hand planes like the Faithful No. 3 to square edges before joinery. Remember: adapting to wood’s nature creates heirloom-quality work that stands the test of time.
Mastering the Dovetail Joint by Hand
Perfect dovetail joints are the hallmark of skilled hand tool joinery. These interlocking pins and tails create strong, durable connections using traditional woodworking techniques that have stood the test of time. Whether building a drawer or a box, this joint demands precision but rewards patience. Start with straight-grained woods like walnut or mahogany for the pin board, paired with lighter woods like basswood for tails to highlight joinery craftsmanship.
Begin layout by marking baselines with a marking gauge. Use a hand tool joinery tips favorite—Spear and Jackson’s 10-inch dovetail saw—to cut tails first, ensuring saw teeth align with grain. A 15 PPI blade reduces tear-out, while a 3/8-inch chisel and joiner’s mallet remove waste. Trace tail patterns onto the pin board with a marking knife, then repeat the saw/chisel process for pins. Test fit frequently, sliding pieces together to check alignment. A flashlight helps spot gaps in corners.
Common pitfalls include uneven spacing and chisel tear-out. Prevent splits by leaving baseline marks slightly proud. For misaligned pins, double-check your layout angles with a sliding bevel gauge. Always use sharp chisels ground to 12° skew for clean corner work. Practice on scrap wood first—mastering this joint builds confidence in traditional woodworking techniques. Remember, even Disston’s fruitwood-handled saws require patience to learn their unique flex. Every mark and cut refines your skill, turning raw wood into lasting craftsmanship.
The Art of the Mortise and Tenon Connection
At the heart of handcrafted joinery methods lies the mortise and tenon joint—a timeless connection used in tables, doors, and frames. This robust joint pairs a projecting tenon with a matching mortise hole, ensuring strength without modern machinery. Traditional wood joinery tutorials often highlight this as a foundational skill for artisans.
- Layout: Use a try square and marking knife to scribe shoulders. A mortise gauge marks cheeks for even width.
- Cut tenons with a handsaw, trimming excess with a chisel for clean shoulders.
- Drill mortise holes with a brace and auger, then clean walls with a chisel.
- Test fit joints, adjusting with paring cuts. Drawbore holes with a dowel and mallet to pull pieces tight.
Explore variations to suit your project:
Variation | Description | Use |
---|---|---|
Through Tenon | Visible on both sides | Chair legs, table aprons |
Wedged Tenon | Slotted for wedges | Outdoor structures, timber framing |
Fox Tenon | Half-tenon design | Lightweight joinery |
Sharp tools and patience are key. Always dry-fit joints before assembly. These handcrafted joinery methods build furniture that lasts generations. Resources like Woodworkers Guild of America offer detailed guides for mastering this classic technique.
Creating Strong Box Joints Without Electricity
Box joints are vital for sturdy, attractive boxes and drawers. Mastering them with hand tools offers precision and control. Here’s how to craft them using traditional methods, ensuring joints that outlast mass-produced alternatives.
Layout and Marking Techniques
Start by laying out finger joints with precision. Use a marking gauge to score the baseline, then dividers to space fingers evenly. A marking knife and combination square ensure clean lines. For example:
- Marking gauge: sets initial depth for fingers
- Dividers: space fingers uniformly
- Combination square: confirms 90° angles
Saw Selection and Cutting Strategies
Choose a fine-toothed back saw for straight cuts. Here’s how to proceed:
- Score lines with the saw, following marked guidelines
- Use a coping saw to remove waste between fingers
- Test cuts against a straightedge to check alignment
Cleaning Up Box Joints with Hand Tools
A table summarizes key tools for refining joints:
Tool | Purpose |
---|---|
Jack Plane | Flattens joint edges |
Bench Chisels | Clean out rough cuts |
Wooden Mallet | Gentle striking for chisels |
Test fits often to adjust as you go. A block plane trims final gaps for a snug fit. These hand tool joinery tips ensure joints withstand daily use. Unlike power tools, hand-cut box joints let you adjust each step, perfect for custom projects like jewelry boxes or storage trays.
Traditional Finishing Techniques for Joinery Projects
Finishing enhances handcrafted joints while preserving the integrity of traditional woodworking techniques Artisanal joinery practices rely on natural finishes that protect wood without masking its natural beauty. Tung oil, a favorite among woodworkers, penetrates deeply and retains wood’s original color, making it ideal for showcasing hand-cut details.
Finish | Application | Drying Time | Key Advantage |
---|---|---|---|
Tung Oil | Brush or cloth | 24-48 hours | Non-toxic, highlights wood grain |
Linseed Oil | Brush | 24 hours | Affordable, deep penetration |
Shellac | French polish | 1-2 hours | Repairable with alcohol |
Beeswax | Buffed on | Immediate | Softens harsh edges |
Milk Paint | Brush | 1-2 hours | Eco-friendly, vintage look |
For smooth application, try these tips: wrap sandpaper around a scrap wood block to sand curves. A leather glove with painter’s tape holds sandpaper securely during shaping. Credit cards work as makeshift spreaders for even glue distribution. Always start with 220-grit sandpaper before applying finishes to ensure a smooth surface.
Traditional finishes like tung oil and shellac develop a natural patina over time, contrasting with modern polyurethane’s plastic look. These methods are often repairable—like touching up shellac with a rag and alcohol—without sanding down layers. Choose finishes based on project use: shellac for high-traffic surfaces, wax for decorative pieces.
Japanese Joinery Methods Worth Adopting
Traditional wood joinery tutorials often overlook the precision of Japanese techniques, yet their minimalist elegance offers fresh inspiration. These handcrafted joinery methods prioritize harmony between material and form, blending utility with artistry.
Japanese joinery philosophy centers on compression and tension, using wood’s natural properties to create enduring bonds without metal fasteners. This approach emphasizes the “absence of noise,” where joints remain visually subtle while showcasing wood’s beauty. Techniques like soaking wood in water before cutting, as practiced in traditional tutorials, enhance grain alignment for smoother cuts.
- Ryobi Japanese pull saws (dozuki) for clean, controlled cuts
- Oire nomi chisels for precise shaping
- Kanna planes with wooden bodies for smooth surfaces
Mastering a basic tsugite joint involves three steps:
- Mark reference lines using a sumitsubo marking compass
- Cut mortises with pull strokes using a chisel
- Test-fit joints incrementally for perfect alignment
Anna Antropova’s research highlights how Japanese methods like “search for lightness” reduce material waste, creating slim, functional designs. Even Western woodworkers can adopt these principles by integrating pull-cut tools into their workflow. Exploring these handcrafted joinery methods not only expands technical skills but reconnects with centuries-old craftsmanship values.
Troubleshooting Common Hand-Cut Joinery Problems
Every woodworker, even experts, faces setbacks when working with hand tools. Here’s how to solve three common issues without sacrificing craftsmanship:
Fixing Gaps in Your Joints
- Use thin shims between joints during clamping to distribute pressure evenly
- Apply clamps perpendicular to gaps for maximum compression
- Fill minor gaps with traditiona-joinery-without-power-tools-tips-41 techniques like tapered tongues or sliding fits
Dealing with Tearout During Cutting
“A sharp chisel is your best defense against tearout,” says master craftsman James Krenov. Maintain tools with regular honing. Use a sacrificial backing board when drilling or boring. Light paring cuts with a block plane smooth damaged surfaces.
Adjusting Joints Too Tight or Loose
For overly tight joints:
- Use a shoulder plane to pare tenons 1/32″ at a time
- Test fit frequently to avoid over-shaving
For loose joints:
- Insert tapered wedges in mortise-and-tenon joints
- Reinforce with hand tool woodworking tips like splines or glue blocks
Remember: Most issues stem from tool sharpness or wood prep. A shooting board and marking gauge ensure accurate layouts. When in doubt, prioritize patience over force—precision comes with practice.
Incorporating Decorative Elements in Traditional Joinery
Traditional joinery isn’t just about strength—it’s a canvas for creativity. Artisanal joinery practices turn functional connections into visual highlights. From exposed through tenons to intricate dovetails, these elements can become focal points in furniture.
Begin by highlighting joints naturally. Through-mortise and tenon joints show craftsmanship when left visible. Dovetail tails in contrasting wood species add color and texture. Splines or geometric inlays between glued joints create patterns without weakening structure.
- Use carved edges on joint surfaces: beads, chamfers, or scrollwork.
- Add decorative keys like butterfly inlays to mend cracks while adding charm.
- Experiment with stringing—thin wood strips along joint lines for subtle contrast.
Traditional woodworking techniques thrive when decoration serves purpose. A Japanese tsugite joint, for instance, combines locking mechanics with geometric artistry. Balance is key: avoid overcomplicating joints that bear heavy loads. Start simple—add a bead along a dovetail’s edge or stain contrasting wood for a miter joint.
Decorative elements should never sacrifice strength. Test joints under stress before adding carvings. Online guides like Wood Magazine’s decorative joinery series offer step-by-step examples. Let form and function work together, and your pieces will reflect centuries of skilled craftsmanship.
Building Your First Project Using Only Traditional Joinery
Starting with a simple project builds confidence in woodworking without power tools. Choose a project that teaches core skills while staying achievable. A tool tote combines dovetails, dados, and tenons—all using hand tools.
Project Selection for Beginners
Pick a project that balances skill and complexity. Small boxes, shelves, or a tool tote work best. Look for plans that use 2-3 joint types. Avoid projects needing advanced cuts until basics are mastered.
Creating a Simple Tool Tote with Multiple Joints
Follow these steps to build a functional tote:
- Use a Ryobi Japanese hand saw to cut 1/4″ thick pine boards.
- Mark dovetail joints with a pencil and marking knife for drawer fronts.
- Chisel out mortises for the tote’s base using a Japanese water stone-sharpened chisel.
- Test-fit joints before final assembly for a tight fit.
Tool | Description |
---|---|
Ryobi Japanese Hand Saw | Cuts precise joints without electricity. |
Japanese Layout Square | Ensures 90-degree angles for clean joints. |
Wooden Mallet | Safely drives chisels without marring wood. |
Block Plane | Trims edges for smooth, even surfaces. |
Lessons Learned from Your First Hand-Tool Project
- Sharp tools save time—honed edges reduce effort.
- Test fit joints early to catch mistakes before final assembly.
- Use clamps to hold pieces steady during glue-up.
Every mistake teaches hand tool joinery tips, like how to fix gaps with a chisel or smooth tearout with sandpaper. Celebrate progress—each project builds skill!
Conclusion: Continuing Your Journey with Traditional Joinery
Traditional-joinery-without-power-tools-tips-41 highlight how hand tool woodworking tips can transform your craft. From dovetails to mortise-and-tenon joints, this guide has shown how intentional focus and patience unlock timeless techniques. Every cut made with a hand saw or chisel connects you to centuries of craftsmanship, a tradition practiced by millions worldwide.
As you advance, explore complex joints like Japanese tsugite or refined box joints. Online communities like the United States-based Traditional Woodworker’s Guild or books like “The Anarchist’s Tool Chest” offer pathways to deepen skills. Remember, even modern tools like the Leigh FMT or Festool Domino can complement handwork without sacrificing tradition.
Wood’s natural behavior demands respect. Prioritize planning, starting with small projects like tool totes before scaling up. Balance your process: bandsaws for safe rips or routers for precision grooves can coexist with hand methods. Each project sharpens your ability to read grain and anticipate movement.
Preserve this art by sharing knowledge with newcomers. The joy lies in the meditative rhythm of hand tools—chiseling, fitting, and creating heirlooms that last generations. By mastering these skills, you ensure traditional joinery endures, blending intentionality with the quiet satisfaction of work well done.
FAQ
What is traditional joinery without power tools?
Why are hand tool skills important in woodworking?
How can beginners start learning traditional joinery techniques?
What types of wood are best for traditional joinery?
What tools should I have for traditional woodworking projects?
How do I avoid common mistakes while making hand-cut joints?
What are the sustainability benefits of traditional joinery techniques?
Can I integrate modern tools with traditional joinery techniques?
What is the significance of Japanese joinery in woodworking?
How can I troubleshoot joinery problems I encounter?
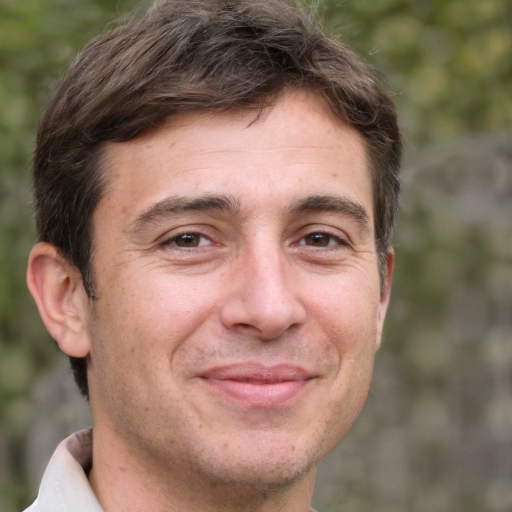
Oliver Bennett is a passionate craft writer and eco-conscious woodworker, specializing in rustic décor, sustainable projects, and handmade wooden toys. He shares practical tips and timeless inspiration for homes that value creativity and natural materials.