Did you know that a single pair of Eifel FLASH pliers can grip with 1-ton strength using a unique gear mechanism? That engineering marvel isn’t just a relic—it’s a testament to the craftsmanship embedded in antique hand tools. Today, vintage tool refurbishment transforms these forgotten treasures into functional masterpieces, blending history with practicality. With the right materials like citric acid, jojoba oil, and nylon abrasive pads, even rusty, century-old tools can regain their original precision.
Restoring antique hand tools isn’t just about cleaning rust or sharpening blades. It’s about honoring the legacy of craftsmanship. Proper antique hand tool restoration can turn a dusty plane or chisel into a tool that outperforms modern versions. By using techniques like soaking in vinegar solutions or flattening soles with spray glue and sandpaper, restorers revive both function and beauty. This guide explores how traditional methods ensure these tools remain vital in today’s workshops, whether you’re a woodworker or a collector.
Every step—from removing patina with 0000 steel wool to applying Boeshield protection—preserves history while enhancing usability. Discover how vintage tool refurbishment bridges past and present, turning forgotten tools into trusted companions for generations.
Understanding the Value of Vintage Hand Tools
Old tools carry more than just practical use—they tell stories. Each mark and patina whispers of centuries of craftsmanship. Antique tool restoration experts know this well, preserving history in every restored plane or chisel.
“I love using old tools previously owned by a maker whose skill I’ll never reach. Their work lives on in the furniture I build today.”
Historical Significance of Craftsman Tools
Tools from the 18th and 19th centuries often used materials like rosewood or iron forged with techniques lost to modern methods. Museums like the Mercer Museum display such pieces, highlighting their role in shaping industries. Their value rises when linked to historical events or renowned craftsmen.
Factor | Impact on Value |
---|---|
Age | Tools from pre-Industrial Revolution periods command higher prices |
Rarity | Limited-production tools like 19th-century boxwood planes |
Materials | Rosewood handles or wrought iron add rarity |
Why Antique Tools Often Outperform Modern Counterparts
Many antique tools outlast modern versions. Their steel was forged with slower, layered techniques, creating blades that hold edges longer. Professional tool restoration can revive these qualities, making them as functional as they were centuries ago.
- Metallurgy: Pre-1940s steel often surpasses mass-produced alternatives
- Design: Ergonomic handles shaped by generations of use
- Repairability: Parts were made to be replaced, not thrown away
The Growing Market for Restored Vintage Tools
Auctions now see 19th-century chisels selling for thousands. Professional tool restoration turns neglected heirlooms into collectibles. Tools linked to famous carpenters or historical events fetch premium prices, blending utility with investment potential.
Restored tools aren’t just for collectors—they’re trusted by modern woodworkers for their precision. This blend of history and utility keeps demand rising, proving that old tools still shape our world today.
Essential Equipment for Your Restoration Workshop
Starting a workshop for hand tool repair services or historic tool restoration services requires the right tools and materials. Begin with basic cleaning supplies: dish soap, water, and nylon abrasive pads. Avoid metal pads to prevent scratching. Use citric acid or white vinegar in large receptacles to soak rusted tools. Protective gear like rubber gloves and eye protection are vital when handling chemicals.
- Cleaning tools: Old toothbrushes, 0000 steel wool, and brass brushes tackle crevices.
- Rust removal options: Evapo-Rust, citric acid, or vinegar solutions. For tougher rust, vibrating palm sanders or wire brushes work.
- Sharpening tools: Bench vises, sharpening stones, and a blow-torch for frozen bolts.
- Finishing touches: Mineral oil or citrus wax protect wood, while japanning mixtures (turpentine, asphaltum, boiled linseed oil) recreate original finishes.
“Patience and the right tools turn forgotten tools into treasures,” says a master restorer. “Always prioritize preserving historic details.”
Storage solutions like waterproof bins keep projects safe. For wood handles, sandpaper and sanding blocks refine surfaces. Avoid harsh chemicals on delicate parts. Remember: even small details, like recreating serial numbers with metal foil tape, add authenticity. Every piece deserves care to honor its craftsmanship.
Identifying Antique Hand Tools Worth Restoring
Shopping for the right tools to restore starts with knowing what to look for. Restoring old hand tools isn’t just about fixing metal and wood—it’s about spotting pieces with history and value. Whether hunting flea markets or online, certain clues guide smart choices.
Recognizing Quality Makers and Manufacturers
Tools stamped by renowned brands like Disston, Stanley, and Japanese nomi makers hold higher value. A Disston Victory saw, for instance, fetches £154, while Norris planes with Brazilian rosewood handles can reach £8,000. Look for original logos, patents, or serial numbers. Collectors prioritize tools from pre-WW2 eras, as craftsmanship peaked before mass production diluted quality.
Assessing Tool Condition and Restoration Potential
Tools with natural patina—like aged handles or surface rust—are often more valuable than overly restored pieces. Use this checklist:
- Check for structural integrity: Bent blades or cracked handles may signal poor repair prospects.
- Look for original finishes: Unpainted steel or untouched rosewood grips add value.
- Verify functionality: A chisel that still cuts wood after cleaning shows potential.
Spotting Rare or Collectible Specimens
Rarity drives value. Miniature salesman plows (up to £4,000), or scythes with provenance from historic sites attract collectors. A table summarizes key factors:
Tool Type | Price Range | Key Features |
---|---|---|
Wooden Planes | £200–£8,000 | Rosewood infills, Norris or Record brands |
Vintage Saws | £160–£240 | Original blades, maker’s marks |
Antique Chisels | £1,599+ | Japanese designs, exotic wood handles |
Focus on tools with original parts and minimal prior restoration. Tools linked to historical events or makers like Robert Sorby or Record add instant appeal. When in doubt, prioritize pieces that balance condition and collectibility.
The Art of Antique Hand Tool Restoration: Step-by-Step Process
Restoring vintage hand tools begins with meticulous preparation. Start by photographing every angle of the tool, noting wear patterns and original finishes. These records form a baseline for tracking progress. Professional restorers often use close-up shots to capture details like rust spots or wood grain before cleaning begins.
Documentation and Photography Before Beginning
Create a timeline of your work by logging dates and materials used. Jot down maker marks or patent dates—these details add value during resale or appraisals. Use a smartphone or camera to document even minor cracks or tool marks.
Disassembly Techniques for Different Tool Types
Loosen corroded joints with penetrating oil like PB Blaster or Kroil. For stuck wooden handles, soak the tool in white vinegar for 12–24 hours to weaken rust bonds. Use a bench grinder’s wire wheel to remove loose rust, then sand remaining stains with 80-grit paper. Common tools needed include:
- Vise grips and punch set
- Belt sander with 120-grit belts
- Ball-peen hammer and hacksaw
- Bench grinder with wire wheel attachment
Creating a Restoration Plan
Before cleaning, decide if the tool will be used actively or displayed. Working tools may need reinforced handles made from hickory or beech, secured with brass pins and boiled linseed oil. For antique hand tool restoration projects, prioritize preserving original parts unless they’re unsafe. Always test moving parts like plane blades or chisels for functionality after reassembly.
When replacing handles, match the original wood type using reclaimed oak or hickory. Mark disassembled components with numbered labels to avoid confusion. A written plan should outline steps like rust removal methods, finish choices, and whether patina will be preserved versus fully restored.
Cleaning Methods That Preserve Historical Integrity
Proper cleaning is the first step in vintage tool refurbishment. Start by brushing off loose debris with a soft bristle brush or vacuum. Test any cleaner on a small area before full application to avoid damaging finishes.
- Remove rust gently with a wire brush or a vinegar-baking soda soak (24 hours max).
- Clean metal surfaces with dish soap and water, avoiding wooden handles. Dry immediately to prevent rust.
- For wood, use a damp cloth with vinegar or olive oil—never submerge handles. Wipe dry to avoid warping.
- Apply protective finishes like Soapstone Sealer for metal or Hemp Oil for wood after drying. Let cure 5–7 days.
“The goal is to reveal original surfaces without stripping historical patina,” advise professional hand tool repair services. “Always prioritize reversible treatments.”
Metal parts can use mineral spirits for grease, but wooden handles need extra care. Test oils like Pure Tung Oil first—they penetrate without damaging aged wood. Never use harsh abrasives on stamped markings or delicate engravings.
Protecting historical integrity means balancing cleanliness with preservation. Using gentle methods ensures tools retain their patina and original materials, maintaining both function and collectible value. Always let tools dry fully before applying any finishes.
Rust Removal Techniques for Vintage Metal Tools
Rust eats away at metal tools, but the right methods can save them. Professional tool restoration experts recommend balancing effectiveness and preservation. Start by assessing rust severity to choose the best approach.
For chemical solutions, mix 2 tablespoons of citric acid with 3 cups warm water. Soak tools up to 24 hours—bubbles mean it’s working. Rinse and scrub with coarse steel wool. Vinegar soaks work too, but take longer. Evaporust removes rust cleanly but costs $20/gallon. Naval Jelly is cheaper at $4/8 oz, but use gloves—it’s harsh on metal.
Method | Pros | Cons |
---|---|---|
Citric Acid | Wood-safe, fast | Time-sensitive soak |
Vinegar | Affordable, reusable | Slower |
Electrolysis | Deep clean | Risk of embrittlement |
Mechanical methods include wire brushes for loose rust and sandpaper for fine touch-ups. Avoid electrolysis on edged tools—it weakens blades. Always test small areas first. Steel wool (grade 1) works well for hand tools. For heavy rust, a disc sander with 100-grit abrasive strips away stubborn layers.
“Preserve patina on collectible tools—it adds historical character,” advises antique tool restoration experts. Light surface rust can stay if it doesn’t compromise structure.
Deciding between full removal and partial retention requires skill. Professional tool restoration shops use electrolysis for extreme cases but avoid it for delicate items. Always prioritize preserving original materials. Whether using vinegar or citric acid, rinse thoroughly and apply oil to prevent regrowth.
Restoring Wooden Components: Handles, Planes, and Boxes
Wooden parts like handles and planes hold the soul of historic tools. Whether repairing a split plane body or restoring a worn handle, antique woodworking tool restoration requires balancing preservation and functionality. Start by assessing damage—original wood retains historical value, so repairs should blend seamlessly with existing wear.
Wood Cleaning and Refinishing Approaches
Clean surfaces gently with Kotton Klenser to remove grime without stripping finishes. For deeper cleaning:
- Soak in mineral oil overnight to soften old finishes.
- Sand with 100-120 grit, progressing to 320 grit for smoothness.
- Apply a final coat of Johnson’s Paste Wax to protect the grain.
Grit | Use |
---|---|
100-120 | Initial smoothing |
220-320 | Final polishing |
Handle Repair and Replacement Considerations
When replacing handles, match original designs—American tools favor centered grips, while European styles often position handles near the end. Use beech or applewood for authentic materials. For minor cracks:
- Fill gaps with epoxy, then sand flush.
- Secure joints with hide glue for historically accurate repairs.
Traditional Finishes for Authenticity
Preserve patina where possible. For worn surfaces, apply tung oil or shellac to mimic original finishes. Stanley Planes often used natural oils, so avoid modern polyurethane unless restoring for display. Professional historic tool restoration services can advise on balancing preservation and usability.
Sharpening and Tuning Antique Cutting Tools
Restoring old hand tools isn’t complete without bringing their edges back to life. Proper sharpening transforms a restored tool from a display piece to a functional treasure. Start by flattening the blade’s back until it’s dead flat—a crucial step often overlooked. This ensures even contact when sharpening the bevel.
- Use a bench grinder with a hard felt buffing wheel to shape the bevel. Hold the blade tangent to the wheel to avoid overheating.
- Hone the edge on oil or water stones, following angles specific to the tool type. A 25-degree angle works for most chisels and plane irons.
- Strop the blade on leather with polishing compound for a razor-sharp finish.
For vintage tool refurbishment to succeed, tuning mechanical parts like plane frogs and lever caps is vital. Adjust frog positioning to align the blade properly. Test alignment by holding the tool blade against a light source—no gaps should appear between the blade and body.
Old scissors revive easily: clean rust with fine-grit sandpaper, then apply light machine oil. Test blades by cutting layered paper. For detailed guidance, consult books by Lie-Nielsen Tools, Leonard Lee’s The Complete Guide to Sharpening, or Ron Hock’s Knife and Tool Sharpening.
Regular testing ensures peak performance. Drag the edge across newspaper—if it tears the paper, sharpening needs adjustment. Properly tuned tools will glide through wood effortlessly, proving your restoration succeeded. With care, these heirlooms regain their original precision, ready for another century of use.
Preserving and Protecting Your Restored Tool Collection
Maintaining restored tools ensures they stay in top condition for generations. Proper preservation combines smart storage, regular upkeep, and protective treatments. Whether you use them daily or display them as collectibles, ongoing care keeps these heirlooms functional and beautiful.
“True preservation lies in balancing accessibility and protection—every tool deserves respect after its journey.” — Antiques Conservators Society
Climate Control and Storage Solutions
Store tools in dry areas with humidity under 50%. Use silica packets in sealed containers for metal parts. For wood handles, apply jojoba oil every 6 months—its non-greasy formula resists sawdust buildup. Boesheild T-9 spray guards metal surfaces from moisture. Like hand-carved kitchen tools, wooden handles need periodic oiling to prevent cracking.
Ongoing Maintenance Routines
Follow these steps monthly:
- Wipe metal parts with a cloth soaked in WD-40 to repel water
- Use vinegar to clean rust spots lightly before they worsen
- Apply pure tung oil to wood surfaces for water resistance
Displaying Your Restored Treasures
Showcase tools in glass-front cabinets to allow viewing while blocking dust. Use scrap garden hose pieces to protect blade edges during storage. Rotate displayed tools occasionally to ensure even exposure. Professional hand tool repair services can create custom display stands for rare pieces.
Patience is key—let finishes cure fully before use. Regular checks for tight fittings and clean moving parts maintain smooth operation. Proper care honors both the tool’s history and your restoration work.
Conclusion: Honoring Craftsmanship Through Restoration
Restoring an antique hand tool isn’t just fixing metal or wood—it’s a conversation with history. Each repaired tool carries the legacy of its maker, bridging past and present skills. By learning traditional methods, modern crafters honor the patience and precision of earlier artisans. This work turns forgotten tools into functional heirlooms that teach us the value of durable, timeless design.
Communities of restorers online and in workshops share tips, from cleaning rust to sharpening blades. Watching a rust-crusted plane regain its gleam reminds us that these tools aren’t just relics—they’re proof of human ingenuity. Every restored chisel or saw becomes a lesson in patience and care, showing how old tools can outlast modern disposables.
When projects feel beyond your skills, historic tool restoration services offer expertise in preserving authenticity. Professionals use period-correct materials, ensuring tools stay true to their origins. Their work protects both the tool’s value and its story, whether fixing a 19th-century lathe or a chisels’ handle. These services keep traditional techniques alive for future generations.
Every restored tool is more than a finished project—it’s a promise to sustain heritage. By choosing repair over replacement, we reject today’s throwaway culture. These tools remind us that craftsmanship endures. Their stories live on when we value care over convenience, ensuring the spirit of hands past continues to shape our world today.
FAQ
What is antique hand tool restoration?
Why should I consider restoring vintage hand tools?
What materials do I need for my restoration workshop?
How do I identify which antique tools are worth restoring?
What is the step-by-step process for restoring an antique hand tool?
What cleaning methods best preserve the integrity of antique tools?
How can I effectively remove rust from vintage metal tools?
What are the best practices for restoring wooden components in antique tools?
What techniques should I use for sharpening and tuning antique cutting tools?
How can I preserve and protect my restored tools?
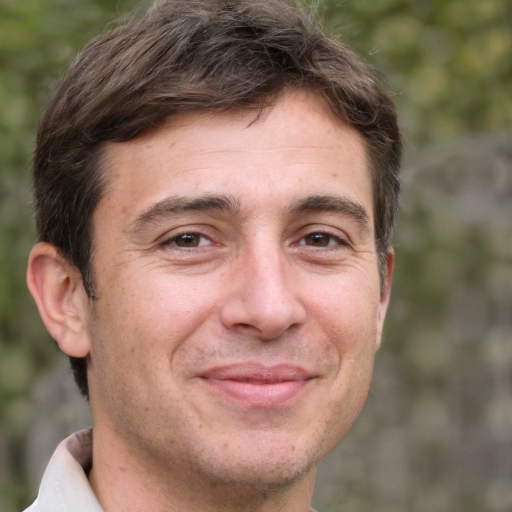
Oliver Bennett is a passionate craft writer and eco-conscious woodworker, specializing in rustic décor, sustainable projects, and handmade wooden toys. He shares practical tips and timeless inspiration for homes that value creativity and natural materials.