Did you know that pocket-hole joints—crafted with just a drill and jig—can assemble a wooden table in minutes without a single clamp? This modern method mirrors ancient techniques like mortise-and-tenon joints, used for over 4,000 years to build furniture that lasts generations. Traditional woodworking techniques remain vital today, proving that wood joinery without machines can rival power-tool projects in strength and elegance.
Wood joinery without machines relies on tools like the Ryobi Japanese handsaw and layout squares to create heirloom-quality furniture. This guide teaches methods from simple butt joints to intricate dovetails using only hand tool woodworking. Discover how traditional techniques like mortise-and-tenon or modern pocket-hole systems turn raw wood into masterpieces, combining durability with artistry.
Whether building a bench or a cabinet, this article reveals how traditional woodworking techniques ensure lasting results. From marking with a pencil to paring with a block plane, every step highlights the satisfaction of crafting without machinery. Let’s explore why hand tool woodworking remains the gold standard for furniture that blends strength, beauty, and the timeless art of joinery.
The Lost Art of Hand-Crafted Wood Joinery
Handcrafted wood joinery remains a testament to craftsmanship that transcends time. These methods, passed down through generations, blend history with practicality in today’s fast-paced world.
Why Traditional Joinery Methods Still Matter Today
Antique joinery techniques like mortise-and-tenon and dovetail joints endure because they outlast modern fasteners. Christopher Schwarz notes in The Workbench Book that these methods ensure longevity by avoiding nails or screws prone to rust or stripping. Key components like holdfasts and bench screws, as detailed in Joseph Moxon’s 17th-century texts, still anchor wood securely during shaping. Traditional tools like the fore plane, with its curved iron, maintain precision without electricity.
The Unique Character of Hand-Joined Woodwork
Method | Characteristic |
---|---|
Handcrafted wood joinery | Visible grain patterns and slight irregularities |
Machine-made joints | Perfectly uniform but often sterile in appearance |
Artisan wood joinery leaves a signature in every piece. Dovetails and lap joints show the maker’s skill, creating heirlooms with soul. Unlike factory lines, these imperfections tell stories of human hands shaping wood.
Environmental Benefits of Machine-Free Woodworking
- No electricity use reduces carbon footprint
- Reclaimed wood projects minimize waste
- Repairable joints extend furniture lifespan
3D-printed jigs modernize without sacrificing tradition, while hand tools produce zero dust compared to power equipment. As Jennie Alexander advocates in Make a Chair from a Tree, working by hand aligns with sustainable practices. Every mortise carved becomes a step toward eco-friendly craftsmanship.
Essential Hand Tools for Creating Beautiful Joinery
Every joinery project starts with the right tools. Whether mastering joinery methods without power tools or building handmade joinery craftsmanship, these essentials ensure precision and durability.
Must-Have Saws for Precision Cutting
Begin with the right saws. Japanese pull saws like the Ryobi model excel for clean, controlled cuts. Pair them with a Western dovetail saw for delicate work. A panel saw handles general cuts, while a back saw ensures accuracy in joints. Look for blades with fine teeth (10-15 TPI) for tight-fitting joints.
Chisels and Gouges: Your Shaping Toolkit
Chisels are the workhorses of hand tool woodworking. Start with a 1/4”, 1/2”, and 3/4” bench chisel set. Add a 1-inch bevel-up chisel for paring. For curved cuts, use gouges. Always keep edges sharp with a Norton double-sided oil stone. A Thor mallet delivers controlled strikes without damaging tools.
Measuring and Marking Tools for Accuracy
- A 6-inch rule and combination square form the basics for layout
- Use a marking knife and pencil for crisp lines
- Marking gauges and mortise gauges transfer dimensions precisely
- A 25-foot tape measure handles larger projects
Mallets, Hammers and Striking Tools
Choose striking tools carefully. Wooden mallets like the Thor brand protect delicate surfaces, while brass hammers suit softer woods. Avoid steel-faced hammers for chiseling to prevent damage. Pair tools with a No.5 Jack plane for smoothing edges and end grain. A router plane corrects mistakes quickly.
Setting Up Your Hand Tool Workspace
Your workspace for wood joinery without machines starts with a sturdy workbench. Traditional woodworking techniques thrive in spaces where tools stay organized and movements stay efficient. A bench at 34–36 inches suits most tasks, but adjust height based on your project—lower for planing wood, higher for detailed joinery.
Tool storage options include wall-mounted boards, rolling carts, or drawers. Keep chisels, saws, and clamps within reach. Books like Hand Tools by Aldren A. Watson suggest grouping tools by task. Lighting matters too: natural light paired with LED task lamps reduces eye strain.
- Use pegboards or magnetic strips for quick access to chisels and saws
- Store large tools like workbenches near work areas
- Rotate seasonal projects to organize space efficiently
Even small spaces work. A corner of a garage or spare room becomes a functional area with smart storage. Prioritize safety: always wear goggles and gloves. Regular tool inspections ensure they stay sharp and safe for precise cuts. Whether you’re building a side table or mastering mortise joints, a well-organized space fuels creativity without overwhelming clutter.
Understanding Wood Properties for Successful Joinery
Choosing the right wood and respecting its natural behavior are key to mastering artisan wood joinery. Every tree species reacts differently to moisture and pressure, so knowing their traits ensures joints last decades.
Hardwoods vs. Softwoods for Different Joints
Hardwoods like oak or maple resist splitting, making them ideal for handcrafted wood joinery like mortise-and-tenon. Pine and cedar are softer, better for lightweight projects. Always match the wood’s density to the joint’s stress points.
Working With Grain Direction
Cutting against the grain causes splinters, while following it ensures smooth surfaces. Use a sharp chisel to avoid tear-out when paring end grain. Traditional woodworking techniques rely on aligning grain direction with joint function for strength and aesthetics.
Seasonal Wood Movement Considerations
Wood expands and contracts up to 3/16” per foot in humid conditions. Design joints to move gracefully:
- Use breadboard ends on tables to allow seasonal expansion
- Leave gaps between panels for swelling
- Store wood in a stable 60-70% humidity environment
Monitor with a hygrometer to prevent warping during assembly.
Wood Joinery Without Machines: Basic Techniques
Mastering foundational techniques turns raw wood into lasting structures. These methods build precision using only hand tools, creating joints like mortise and tenon, dovetail, and more. Start with these steps to ensure every cut and carve aligns with your design.
Layout and Marking Fundamentals
Sharp pencils, marking gauges, and combination squares define every project’s blueprint. Use a knife to score lines for saw alignment. A marking gauge ensures consistent measurements, while a square keeps edges true. These steps prevent errors before cutting.
Hand-Sawing Strategies for Clean Cuts
- Hold the saw at a 30-degree angle for smooth push cuts.
- Begin cuts slowly, using your thumb to guide the blade’s edge.
- Alternate forward and back strokes to correct drift from layout lines.
Practice on scrap wood until sawing follows your marked lines effortlessly.
Chisel Work and Paring Techniques
Chisels shape joints by paring wood shavings, not smashing. Grip the tool like a hammer for control, and work with the grain to avoid tear-out. Use a mallet to tap the chisel’s flat back, clearing waste from saw cuts. Safety first: always cut away from hands.
“Precision in paring transforms rough cuts into tight-fitting joints,” say experts in hand tool woodworking.
These techniques build the skills needed for advanced joints like dovetails or box joints. Consistent practice turns basics into second nature, enabling sturdy projects without power tools.
Creating Simple Butt Joints and Lap Joints By Hand
Mastering butt and lap joints forms the backbone of rustic wood joinery. These joints rely on precision handwork rather than machinery, making them perfect for wood joinery without machines. Start with butt joints: align two pieces edge-to-edge, ensuring square cuts with a combination square. Strengthen them by adding hand-cut dowels or splines, techniques that add both strength and visual interest.
- For furniture joinery by hand, use a try square to mark half-lap joints, cutting each piece to half its thickness.
- Sand mating surfaces smooth to ensure tight fits. Test joints with scrap wood before final assembly.
- Use a mallet and chisel to clean up shoulders for a seamless look.
A half-lap joint halves each workpiece, creating flush surfaces. Cross-lap variations overlap boards at 90-degree angles, ideal for chair legs or frame corners. For example, the rustic bench project uses lap joints to attach legs to seats, demonstrating their practicality.
“Lap joints are used to overlap pallet boards at the corners and are secured with screws for a sturdy frame.”
Always cut on the waste side of layout lines to avoid mistakes. Reinforce joints with wood glue and pins for added durability. These methods turn simple connections into foundational elements of sturdy, handmade furniture.
Mastering Traditional Mortise and Tenon Joints
At the heart of traditional woodworking techniques, the mortise and tenon joint is a timeless connection used in everything from chairs to cabinets. This handmade joinery craftsmanship requires precision but rewards patience with joints that endure centuries of use. Begin by mastering these steps to achieve strong, precise fits.
Layout and Marking Your Mortise and Tenon
- Measure mortise width as one-third of the workpiece thickness for optimal strength.
- Mark tenon length to extend slightly beyond the final size—trim later for perfect alignment.
- Use a marking gauge to score lines, ensuring the tenon’s shoulders align perfectly with the mortise’s edges.
Chopping a Mortise Using Only Hand Tools
Start by drilling guide holes with a brad-point bit. Drill halfway from each side to avoid splintering ends. Artisan wood joinery experts recommend keeping holes at least 3/8″ from the workpiece end. Use a mortise chisel to pare along scored lines, working from the center outward. Test the fit frequently to avoid overcutting.
Cutting Perfect Tenons With Hand Saws
Cut tenons with a backsaw, sawing precisely to layout lines. Trim cheeks and shoulders gradually, checking alignment against the mortise. A 1/16″ gap between tenon and mortise allows glue space without excess slop. Sand or plane tenons to eliminate wobbles.
Fitting and Adjusting Your Joints
Slide the tenon into the mortise using hand pressure—no force means it’s too tight. Adjust with a shoulder plane or chisel to refine fits. Wedges or drawbore pins add extra security for heavy-duty projects. Always test joints on scrap wood first.
Handcrafted Dovetail Joints: The Crown Jewel of Artisan Joinery
Handcrafted wood joinery reaches its peak in the delicate art of dovetail joints. These interlocking pins and tails have adorned chests, drawers, and boxes for centuries, symbolizing handmade joinery craftsmanship at its finest. Each slanted angle and precise cut tells a story of patience and skill, making them a hallmark of heirloom-quality furniture.
Begin by mastering furniture joinery by hand basics: layout tools like dividers and marking gauges ensure consistent angles. Start with through dovetails for visible beauty or half-blind joints for subtle strength. Advanced woodworkers might tackle curved or splay-shouldered variations, like the African Padouk buffet’s 127 dovetails or the curved trinket box’s intricate design.
- Use a dovetail layout tool to mark pins and tails accurately
- Saw along layout lines with a backsaw, then pare waste with a chisel
- Practice on poplar or pine scrap wood before tackling oak or exotic species
Projects like the Gerstner-inspired tool chest or black-painted poplar picture frames prove even complex dovetails yield reliable results. Focus on perfect fitting—tight joints require trial fits after each cut. Embrace imperfections as learning tools; even seasoned artisans refine their technique over decades.
Beginners can start with simple boxes, progressing to dressers and desks. The key? Practice patience. Each hand-cut joint becomes a testament to timeless skill—a tradition alive in every well-made piece.
Japanese Joinery Techniques for Furniture Without Fasteners
For over a millennium, antique joinery techniques have shaped Japanese architecture and furniture. The rustic wood joinery methods of Miyadaiku carpenters ensure structures like Horyu-ji Temple stand for centuries. These traditional woodworking techniques use interlocking joints that adapt to stress without nails or screws.
Kanawa Tsugi (Mortise and Tenon Splices)
These end-to-end joints fuse two pieces into a single beam. Used in standing cabinets, they distribute weight evenly. The process involves precise chisel work to fit tenons into mortises with 30-micron accuracy.
Shiguchi Joints for Corner Connections
Corner joints like kama tsugi (gooseneck) and kone tsugi (hip joints) lock frames together. Their angled cuts form self-tightening bonds when stressed. Modern furniture makers use these for rustic wood joinery in chairs and tables where joints bear heavy loads.
Tools Specific to Japanese Joinery
Miyadaiku use pull saws with razor-sharp blades and chisels with hollow-ground backs. Western woodworkers can adapt their tools by sharpening blades to finer angles. Key tools include:
- Pull saws for clean cuts
- Bamboo marking gauges
- Bevel-edged chisels
Wood Type | Properties | Applications |
---|---|---|
Hinoki | Moisture-resistant, fragrant | Outdoor furniture, baths |
Sugi | Weather-resistant, light weight | Frames, shelves |
Kusunoki | Rot-resistant, dense grain | Table legs, structural joints |
Modern makers can blend Japanese methods with hand tools for durable, fastener-free designs. YouTube’s Japanese Architecture: Wisdom of Our Ancestors demonstrates these techniques in action. Whether building chairs or cabinets, these methods prove strength lies in precision—not power tools.
Finishing Touches: Hand-Planing and Surface Preparation
Polishing handmade furniture requires patience and precision. Traditional woodworking techniques shine here, ensuring every piece reflects craftsmanship. Let’s explore methods that turn raw wood into gleaming surfaces without modern machinery.
Bench Planes: The Secret to Glass-Smooth Surfaces
Stanley #4 and #5 planes are workhorses for smoothing. Adjust the blade angle to 60 degrees to remove twists. Use winding sticks to check for warps before final passes. A sharp iron (blade) is key—dull tools leave marks.
Technique | Clarity | Grain Visibility |
---|---|---|
Hand Planing | High | Enhanced |
Sanding | Low | Dull |
Edge Treatments for Handmade Joinery Craftsmanship
- Use a block plane to create clean edges for dovetails or mortises.
- Spokeshaves shape rounded edges quickly—ideal for chair arms or table legs.
- Scrapers smooth end grains to prevent splintering without power tools.
Hand-Sanding for Furniture Joinery By Hand
When planing isn’t enough, sand softly. Start at 120 grit, then 220 for final passes. Use a sanding block to keep edges flat. For curves, wrap paper around a dowel to follow contours.
Pro tip: Re-planing sanded wood boosts finish quality. Tung oil, a natural choice, enhances grain without masking wood’s essence. Apply three thin coats, buffing each with 0000 steel wool. This method aligns with traditional woodworking techniques, preserving the wood’s natural beauty.
Troubleshooting Common Hand-Cut Joinery Problems
Even the most skilled hand tool woodworking practitioners face occasional setbacks. Wood joinery without machines demands precision, but many issues can be fixed with simple adjustments. Let this guide help turn mistakes into learning moments.
“A flawed joint is just a chance to refine your technique.” – Traditional Japanese joinery master
Issue | Fix |
---|---|
Tenons too tight | Pare shoulders slightly with a chisel |
Mortise misalignment | Use a dummy tenon to test and adjust depth |
Splitting in narrow wood | Support workpiece with clamps before cutting |
Loose joint gaps | Add shims made from scrap material |
Remember: Mortise bottoms don’t need flawless surfaces—function matters most. If tenon ends aren’t perfectly square, focus on accurate shoulder measurements instead. Exposed mortises? Add a small shoulder to hide flaws. When chopping mortises, always test with a chisel before final assembly. For undersized tenons, thin shims made from scrap wood can restore proper fit without redoing work.
Prevent issues by always testing joints with dry runs. Keep chisels sharp to avoid tear-out. Use soft mallet strikes when paring. Even joinery methods without power tools allow creative solutions—think of imperfections as part of the craft’s character. Traditional woodworkers relied on these fixes for centuries, turning mistakes into opportunities to refine skills.
Conclusion: Embracing the Rewards of Machine-Free Woodworking
Handcrafted wood joinery connects makers to a timeless tradition rooted in skill and patience. Wood joinery without machines turns every project into a dialogue between wood and craftsperson. The quiet focus required to shape joints by hand fosters a deeper understanding of material and process, unlike any machine-driven approach.
Modern tools like hand planes and chisels remain as effective today as they were centuries ago. The rising demand for traditional tools—like the hand router plane’s price surge from £10 to £150—reflects a growing appreciation for these methods. Tens of thousands of learners, including those inspired by educators who’ve taught 6,500 students and reached 500,000+ via YouTube, prove this craft’s revival.
Artisan wood joinery isn’t just about technique; it’s a philosophy. The Arts and Crafts Movement’s principles—quality, sustainability, and harmony with nature—align with today’s eco-conscious values. Using wood responsibly honors its natural properties, avoiding the Cartesian split between humanity and materials. Simple joints, like dovetails or mortise-and-tenon, demand precision but reward with enduring beauty.
Beginners can start small, practicing layouts with Tage Frid’s guides, then advance to complex projects. Each chisel mark and saw cut builds confidence. The joy lies in mastering techniques that span generations, turning raw wood into functional art. Embrace the rhythm of hand tools—your first project awaits.
FAQ
What is wood joinery without machines?
Why are traditional joinery methods still relevant today?
What unique character does hand-joined woodwork bring to projects?
What are the environmental benefits of machine-free woodworking?
What essential hand tools do I need for creating beautiful joinery?
How can I set up a comfortable workspace for hand tool woodworking?
What fundamental wood properties should I understand for successful joinery?
What are the basic techniques for wood joinery without machines?
What are the steps to create simple butt joints and lap joints by hand?
How can I master traditional mortise and tenon joints?
What are the key points to consider for handcrafted dovetail joints?
What techniques are involved in Japanese joinery without fasteners?
What should I know about hand-planing and surface preparation?
What common problems can arise in hand-cut joinery, and how can I troubleshoot them?
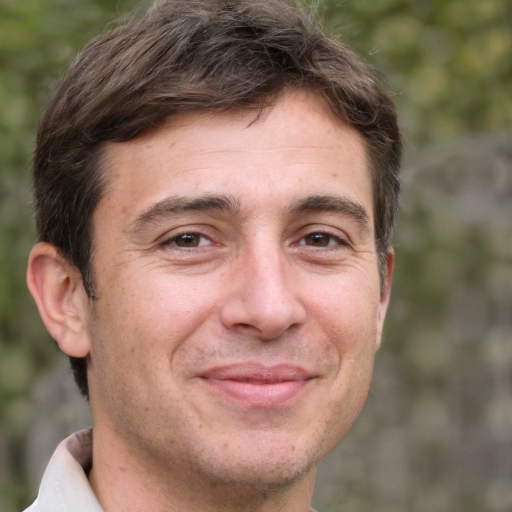
Oliver Bennett is a passionate craft writer and eco-conscious woodworker, specializing in rustic décor, sustainable projects, and handmade wooden toys. He shares practical tips and timeless inspiration for homes that value creativity and natural materials.