Over 5,000 years ago, ancient Egyptian craftsmen were already using dovetail joints to build furniture for pharaohs’ tombs. This age-old technique, named for its resemblance to a dove’s fanned tail, remains a hallmark of fine craftsmanship today. The hand-cut dovetail joint’s enduring legacy lies in its dual role as both a structural marvel and an artistic signature. Historians can trace a piece’s origin or age by studying these joints, making them silent storytellers of woodworking history.
From Egyptian tombs to modern workshops, hand-cut dovetail joints have symbolized excellence. Their interlocking pins and tails—crafted without nails or screws—create strength that outlasts centuries. Even today, brands like Thos. Moser honor this tradition, blending hand-cut precision with modern tools. The dovetail joint history isn’t just about function; it’s a visual language of skill passed through generations, proving why hand-cut dovetail joints still command respect in a world of mass-produced furniture.
The Origins and Evolution of Dovetail Joinery
For over 5,000 years, the dovetail joint history has been woven into human ingenuity. From ancient carpentry to royal workshops, this traditional joinery method has adapted while maintaining its structural brilliance. Today’s techniques echo innovations forged across continents and eras.
Ancient Beginnings: Dovetails in Early Civilizations
Archaeologists unearthed the first examples in Egyptian tombs from 3100 BCE, where cedar chests used dovetails to secure drawer fronts. On India’s subcontinent, a stone pillar at Vazhappally Maha Siva Temple from the 9th century employed dovetails in its construction. Chinese imperial tombs also held lacquered boxes held together by these joints, buried with nobles as symbols of permanence.
Evolution Through Medieval Craftsmen
Medieval European guildssmen turned the dovetail into a craft of mystique. They believed the joint’s interlocking pins formed “spirit traps” that bound the wood’s essence to the piece. A 14th-century carpenter’s manual advised,
“Let the dovetail’s fingers grasp the wood’s soul, lest the piece decay.”
These spiritual beliefs elevated the joint beyond utility, making it a hallmark of skilled craftsmanship.
The Golden Age of Dovetails in 18th Century Furniture
By the 1700s, cabinetmakers perfected the technique into an art. Georgian chests and French commodes displayed intricate hand-cut joints visible on drawer fronts. Masters like Thomas Chippendale used dovetails as signatures, each joint’s angle and spacing tailored to the wood’s grain. This era cemented the dovetail as a mark of luxury, proving that the traditional joinery method reached its artistic peak long before machines changed production.
Understanding the Structural Significance of Hand-Cut Dovetail Joints
“Not only is dovetail joinery beautiful, but it’s functional,” says Thos. Moser craftsmanship experts. “The dovetail is for strength and beauty.”
Hand-cut dovetail joints rely on a simple yet brilliant design. The interlocking pins and tails form a mechanical bond that resists pulling-apart forces. Unlike nails or screws, this dovetail woodworking technique uses no hardware. The angled cuts let wood expand and contract naturally with humidity changes, preventing splits.
- Strength: Angles distribute stress evenly, avoiding weak points.
- Flexibility: Wood movement is accommodated without warping.
- Longevity: No glue needed for the joint’s mechanical grip.
Comparison | Hand-Cut Dovetails | Nails/Screws |
---|---|---|
Strength | Self-locking design | Rely on fasteners loosening over time |
Appearance | Visible geometric patterns | Hidden but less durable |
Longevity | Centuries of proven use | Risk of rust or stripping |
Modern woodworkers still choose hand-cut dovetail joints for heirloom-quality furniture. The hand-cut dovetail joints adapt to wood’s natural shifts, making them ideal for drawers and cabinets. Their design ensures pieces stay strong for generations—proving form and function work together.
Essential Tools for Traditional Hand-Cut Dovetailing
Mastering hand tool woodworking begins with the right equipment. Traditional dovetailing relies on a core set of tools designed for precision. Whether building a chest or a drawer, these instruments ensure clean cuts and tight joints. Let’s explore the essentials.
The Dovetail Saw: Backbone of the Technique
A quality dovetail saw is the heart of this process. Look for a fine-toothed backsaw with 15-20 teeth per inch. The blade should be rigid but flexible, with a handle that fits comfortably. Western saws like the traditional 10-inch handsaw and Japanese dozuki saws (with their pull-cut design) both excel. Key features:
- Western styles: Steel-backed blades for straight cuts
- Japanese styles: Thin blades for precise dovetail angles
- Rip teeth for crosscutting wood grain
Chisels and Marking Tools
Layout accuracy starts with marking tools. A marking gauge with a knife edge (like a wheel gauge) scores clean lines. A marking knife carves precise lines for saw guides. Use a 0.5mm pencil lead for fine lines. Chisels in sizes ¼”, ⅜”, ½”, and ¾” remove waste. See the ideal chisel sizes below:
Chisel Size | Primary Use |
---|---|
¼” | Cleaning narrow pins |
½” | Removing waste between joints |
¾” | Shaping larger tails |
Workholding Equipment for Precision Cutting
A sturdy workbench with a vise is critical. A machinist’s vice or woodworker’s bench vise holds the workpiece firmly. Additions like a shooting board (for squared ends) or a block plane (for finishing) enhance precision. Essential items include:
- Adjustable bench vise
- Woodworking bench with a dead front
- Bevel squares for angle checks
- Clamps for holding pieces
Beginners can start with a basic set: a dovetail saw, 3 chisels (¼”, ½”, ¾”), a marking gauge, and a simple vise. Skill trumps tool quantity in dovetail joint tutorial projects. Practice builds mastery, turning these tools into extensions of your hands.
The Step-by-Step Process of Creating Hand-Cut Dovetail Joints
Mastering this classic technique starts with this practical dovetail joint tutorial. Choose straight-grained wood like pine or mahogany, then use a marking knife and square to transfer layout lines. Every angle and cut matters—precision turns raw materials into functional artistry.
- Layout begins with pencil marks transferred using a marking knife and marking gauge. A sharp knife cleanly defines lines, while a square ensures 90-degree angles for perfect alignment.
- Cutting starts with the pins or tails—many craftsmen begin with pins to avoid overcutting. A dovetail saw (like the Veritas model) follows layout lines slowly, using a bench hook for stability during delicate cuts.
- Chiseling waste requires steady hands. Work from both sides, using a mallet to drive the chisel along waste areas. Alternate chopping and paring to refine the tails and pins without overcarving.
- Assembly uses yellow glue on through dovetails, as Tim Sirois emphasizes. Clamp joints tightly, using a mallet to align pieces before the adhesive sets completely.
“The best hand-cut dovetail joints balance accuracy with the natural wood grain,” says Tim Sirois, highlighting how small adjustments during chiseling refine the final fit.
Practice builds muscle memory for this time-honored craft. Even early attempts yield stronger joints than many modern alternatives. Each step in this dovetail joint tutorial deepens your connection to woodworking history—every chisel strike echoes centuries of tradition. Start slow, embrace imperfections, and let the wood guide your hand.
Regional Variations in Dovetail Joinery Traditions
Woodworking joinery techniques evolved uniquely across cultures, shaped by materials, aesthetics, and local traditions. The traditional joinery method adapted to reflect regional priorities, from European elegance to American practicality.
English vs. Continental European Approaches
English craftsmen favored robustness over delicacy. Their broad pins and fewer tails prioritized sturdiness for heavy furniture. Continental European joiners, like French and German masters, carved finer, denser tails. Through dovetails became a signature in French commodes, while English drawers often used half-blind joints to hide seams.
- English: Broader pins for strength
- European: Delicate tails for decorative appeal
Japanese Dovetail Techniques
“The Japanese pull-saw method redefines precision in woodworking joinery techniques,” notes modern craftsman Theo Cook, popularizing the Japanese Sunrise Dovetail’s compound angles.
Japanese joiners avoided nails, relying on interlocking crossed-dovetails. These hidden joints mirrored cultural values of understated elegance. The pull-saw’s rhythmic cuts produced seamless fits, contrasting with Western showy joints.
American Colonial Adaptations
Colonial woodworkers mixed European methods with New World materials. Pine and oak demanded simpler cuts than European hardwoods. New England chests often had spaced pins for durability, while Southern joiners adopted “lapped” dovetails to save time. These adaptations turned regional styles into markers of origin.
Famous Furniture Examples Showcasing Masterful Hand-Cut Dovetail Joints
Hand-cut dovetail joints have long been symbols of woodworking mastery. From historic treasures to modern masterpieces, these joints blend function and artistry. Explore iconic pieces that define dovetail joint history and inspire today’s craftsmen.
Iconic Period Pieces and Their Joinery
Item | Date | Material | Features |
---|---|---|---|
1780 English Secretary Desk | 1780 | Oak | Drawers with fine hand-cut dovetail joints |
1880s Maple & Cherry Hope Chest | 1880s | Maple/Cherry | Double lid with oversized dovetail joints |
19th-Century Italian Baroque Chest | 1800s | Oak | Heavy dovetails with 2.5″ spacing |
Museum-Quality Examples Worth Studying
Legendary collections like the Victoria & Albert Museum preserve treasures like an 18th-century Italian oak chest (29.93″ H) with bold dovetail spacing. The Metropolitan Museum displays an 1830s English cutlley tray (5.52″ H) where dovetails blend with delicate carvings. Even everyday items like a 1920s baker’s tray (5″ H) show how hand-cut joints adapted to different uses.
Modern artisans like Thos. Moser revive this tradition. Their Dr. White’s Chest uses hand-cut dovetails in Allegheny cherry, proving these joints remain relevant. Studying these pieces teaches today’s woodworkers how hand-cut dovetail joints balance strength and elegance across centuries.
The Decline and Revival of Traditional Joinery Methods
The rise of industrial machinery in the 19th century shifted furniture production from traditional joinery methods toward mass manufacturing. Factories prioritized speed over craftsmanship, replacing hand-cut dovetails with simpler joints. Innovations like the circular saw and steam-powered tools made traditional woodworking joinery techniques seem outdated. Even patented mechanized dovetail jigs emerged, aiming to mimic handwork but lacking its artistry.
Yet, the Arts and Crafts Movement of the late 1800s sparked a counter-movement. Pioneers like William Morris championed handcrafted pieces, valuing visible joinery as proof of skill. This ethos laid groundwork for today’s artisans who blend old and new: CNC machines like the Hundegger K2i now produce precise dovetails, merging efficiency with traditional aesthetics. These tools enable small businesses to replicate complex joints at scale, as seen in the K2i’s capacity to handle 2,000 m³ of timber annually.
Modern woodworkers now learn woodworking joinery techniques through online courses and hand tool brands like Lie-Nielsen. While industrial methods dominate, a growing niche values hand-cut joints. Artisans face challenges—like high prices for custom pieces—but thrive in markets valuing uniqueness. The revival isn’t just nostalgia; it’s a fusion of centuries-old skills with modern tech, proving that tradition and innovation can coexist.
Modern Applications and Appreciation of Hand-Cut Dovetail Joints
Today, hand-cut dovetail joints remain a symbol of craftsmanship in an age of mass production. Woodworkers like those at Thos. Moser blend tradition with modern design, using contrasting wood species to highlight the beauty of their dovetail joints. These joints aren’t just functional—they’re a statement of quality.
Contemporary Furniture Makers Preserving the Tradition
Artisans today adapt the dovetail woodworking technique with updated tools while honoring its roots. Innovations like specialized saws and marking knives simplify precision without sacrificing authenticity. For example:
- Modified saws with rip teeth reduce effort for clean cuts.
- Precision gauges and marking tools ensure consistency.
- Painter’s tape guides prevent overcutting, merging old and new methods.
The Artisanal Value in Today’s Mass-Produced World
Hand-cut dovetails thrive in a market craving authenticity. Consumers seek heirloom-quality pieces that tell a story. “You can’t improve on perfection,” says Tim, reflecting Thos. Moser’s commitment to this legacy. These joints outlast glued or machine-made alternatives, proving their timeless value.
“The beauty of hand-cut dovetails lies in their honesty—they show the maker’s skill.”
From custom cabinetry to high-end furniture, the hand-cut dovetail joints endure as a mark of excellence. Their resurgence highlights a growing appreciation for craftsmanship in an era of disposable goods.
Comparing Hand-Cut vs. Machine-Cut Dovetails: Aesthetics and Strength
Hand-cut dovetails and machine-made versions each offer unique advantages. The dovetail woodworking technique done by hand leaves visible saw marks and slight variations, creating a signature of the craftsman. Machine-cut joints show perfect symmetry but lack the organic character of handwork.
Visual Distinctions Between Hand and Machine Work
- Hand-cut joints show uneven spacing and slight asymmetry
- Machine cuts produce flawless, identical pins
- Experienced woodworkers can spot handwork by checking for kerf marks
Structural Integrity Considerations
Both methods create strong joints when executed properly. Hand-cut versions rely on the woodworker’s skill to align the mechanical lock correctly. Machine methods ensure precise angles but may sacrifice the hand tool woodworking tradition’s tactile adaptability. Tests show properly glued joints resist racking equally well regardless of method.
The Debate Among Modern Woodworkers
Traditionalists like James Krenov argue hand-cut joints embody craftsmanship’s soul. Companies like Lie-Nielsen Toolworks support this by making tools for artisans. Meanwhile, shops like Thomas Moser blend methods: “We use routers for consistent geometry,” explains Tim, “but retain the traditional look people value.” Many woodworkers agree: machines save time without sacrificing strength, but handwork remains unmatched for uniqueness.
Conclusion: The Enduring Legacy of the Dovetail in Woodworking Tradition
Dovetail joints have endured for millennia as symbols of skill and heritage. From ancient Irish Dovetail Woodworking’s early medieval roots to today’s workshops, these joints blend function and artistry. Traditional joinery method mastery once required strict apprenticeship trials, reflecting cultural reverence for craftsmanship. In Irish traditions, a poorly cut joint wasn’t just flawed—it risked releasing a wood’s spirit into the world, underscoring the emotional weight behind each cut.
Modern woodworkers now rediscover hand tool woodworking through online communities, reviving techniques once nearly lost. The hand-cut dovetail remains a bridge between past and present, valued for its strength in furniture and its role in preserving Celtic artistry. Even with modern tools, the joint’s interlocking tails and pins honor centuries of tradition, proving time-tested methods still hold value in our fast-paced world.
Whether shaping a drawer in a New York studio or carving a box in Dublin, the dovetail’s elegance endures. Its enduring appeal lies in connecting makers to a legacy of patience and precision. For those seeking more than assembly-line furniture, mastering this joinery method is a chance to carry forward a story older than machinery—a story told in wood, chisels, and the quiet pride of a well-made joint.
FAQ
What are hand-cut dovetail joints?
Why are dovetail joints significant in furniture history?
How do hand-cut dovetails compare to machine-made joints?
What tools do I need to cut dovetails by hand?
What is the process for creating hand-cut dovetail joints?
What are some regional variations in dovetail joinery?
Can you name some famous furniture examples that feature hand-cut dovetail joints?
How did industrialization impact dovetail joinery?
Why is there a resurgence of interest in hand-cut dovetails today?
Is it difficult to learn how to cut dovetail joints by hand?
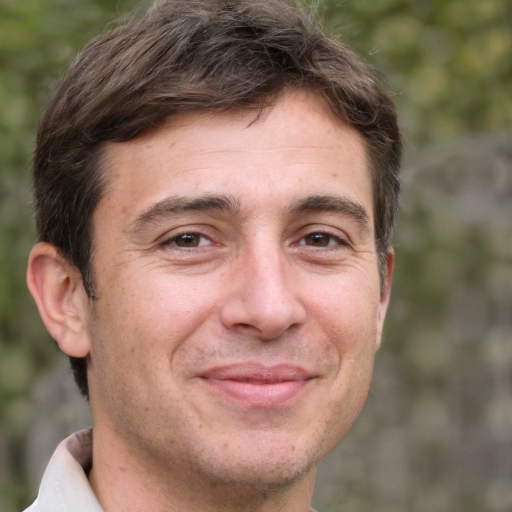
Oliver Bennett is a passionate craft writer and eco-conscious woodworker, specializing in rustic décor, sustainable projects, and handmade wooden toys. He shares practical tips and timeless inspiration for homes that value creativity and natural materials.