Did you know that over 75% of parents prioritize durable, customizable toys for their kids? Custom wooden toy replicas like detailed Viking swords or hand-painted shields offer a lasting alternative to disposable plastic toys. Imagine crafting a sturdy wooden sword with a leather-wrapped handle or a medieval knight’s shield with a steel boss—all tailored to your vision. From designing templates with MDF and spray adhesive to finishing with child-safe stains, this guide breaks down how to create heirloom-quality handmade wooden toys. Whether you’re making a set of two Viking swords for siblings or a single knight’s mace for a collector, every step ensures your creations blend artistry with safety. Let’s dive into transforming raw wood into cherished playthings that stand the test of time.
Starting with simple tools like band saws or routers, even beginners can carve, sand, and assemble intricate designs. Whether you’re etching initials into a sword handle or painting weathered finishes on a shield, this guide covers materials, techniques, and safety tips. Ready to turn your workshop into a creative hub for timeless handmade wooden toys? Let’s begin.
Understanding the Art of Wooden Toy Making
Wooden toys have charmed generations, blending tradition with creativity. Their timeless appeal lies in craftsmanship that bridges past and present. Discover why this art form continues to inspire makers and collectors alike.
The History and Significance of Wooden Toys
Swedish artisans pioneered iconic designs like rocking horses with pine frames and miniature baking sets. These items weren’t just playthings—they taught skills and values. As
wooden toys embody both play and education
, their legacy endures through brands like BRIO, merging mass production with handcrafted charm.
- 19th-century Swedish toys included detailed Noah’s Arks and carved wagons
- Artisans used locally sourced wood, emphasizing sustainability
- Traditional methods like jointed figures and painted decorations remain popular today
Why Custom Wooden Toy Replicas Make Meaningful Gifts
Custom wooden gifts stand out in a digital world. A hand-carved wooden sleigh or a bespoke doll buggy becomes a cherished keepsake. Unlike mass-produced items, these pieces carry stories and care. Parents and collectors prize their durability and uniqueness—perfect for birthdays or heirlooms.
Setting Realistic Expectations for Beginners
Starting small avoids frustration. Beginners should:
- Begin with simple projects like basic blocks or small figurines
- Invest in safety-focused tools for carving and sanding
- Allow ample time for learning curves and design adjustments
Patience is key—masterpieces evolve with practice!
Essential Tools and Materials for Your Workshop
Every custom toy maker needs the right tools to bring unique wooden toy replicas to life. Start with core equipment like band saws for shaping wood and routers for intricate details. A drill press ensures precise holes, while sanders smooth surfaces for a polished look.
- Tools: Band saw, drill press, router, spray adhesive, clamps
- Materials: MDF for templates, hardwood for bodies, dowels for axles, non-toxic paint, and wood glue
Tool Type | Function | Top Brands |
---|---|---|
Band saw | Cuts curves and shapes | Lie-Nielsen Toolworks, Lee Valley & Veritas |
Router | Carves grooves and edges | Bad Axe Toolworks, Robert Sorby |
Sander | Polishes surfaces | Grizzly Industrial, Delta Machinery |
Safety gear like goggles and dust masks are vital. Budget-conscious makers can start with mid-range tools like the Royal 8″ Bench Router before upgrading. For materials, choose poplar or basswood—affordable yet durable options. Always pair wood glue with clamps to ensure strong joints. Remember: quality consumables like 220-grit sandpaper and child-safe acrylic paints make a big difference in final results.
Selecting the Perfect Wood for Your Custom Toys
Choosing the right wood ensures your custom wooden toy replicas are both durable and safe. Let’s explore materials that balance craftsmanship with practicality.
Hardwoods vs. Softwoods: Making the Right Choice
Hardwoods like maple, cherry, and walnut offer strength and detailed finishes, ideal for intricate custom wooden toy replicas. Softwoods such as pine or jackfruit are lighter and easier to carve, perfect for beginners or larger toy pieces. Compare their traits:
- Hardwoods: Durable, fine grain, long-lasting finish
- Softwoods: Lightweight, cost-effective, easy to shape
Non-Toxic and Child-Safe Wood Options
Safety is key when crafting toys for sale. Opt for woods like neem, which has natural antibacterial properties, or jackfruit for smooth painting surfaces. Avoid woods treated with chemicals. For finishes, use water-based or milk paints—both non-toxiс and compliant with toy safety standards.
Sustainable Sourcing Practices
“Sustainable sourcing isn’t just eco-friendly—it’s expected by conscious buyers.”
Choose reclaimed wood or FSC-certified timber to reduce environmental impact. Teak and rosewood are premium choices, but always verify suppliers prioritize ethical practices. Eco-conscious buyers appreciate transparency in sourcing, boosting appeal for wooden toy replicas for sale.
Designing Your Custom Wooden Toy Replicas
Every great project starts with a plan. Designing templates and scaling your ideas ensures your custom wooden toy replicas turn out just right. Start by sketching ideas on paper or using digital tools like sustainable materials to reduce waste. Begin with these steps:
Creating Templates and Patterns
- Sketch basic shapes on graph paper to visualize proportions.
- Transfer designs to wood using carbon paper or chalk lines.
- Test templates with scrap wood before cutting final pieces.
Scaling Techniques for Accuracy
Scaling ensures details stay proportional. Use grids to adjust sizes while keeping shapes intact. For example, a handmade wooden toys train set might need ¼-inch grids to scale wheels and tracks correctly. Proportional dividers help match measurements between templates.
Computer Software for Precision
Software like SketchUp or Tinkercad simplifies complex designs. Here’s how they help:
Method | Pros | Cons |
---|---|---|
Manual Sketching | Cost-effective, tactile feedback | Risk of scaling errors |
Digital Design | Exact measurements, 3D previews | Requires software learning |
Combine both approaches! Many artisans at Brio and NWA Wood Design Shop blend hand-drawn ideas with digital tweaks for polished results. Always test joints and moving parts in software before cutting wood. Remember: precise design saves time and materials.
Step-by-Step Woodworking Techniques for Beginners
Starting with precise measurements is key to crafting personalized wooden toys. Use a bevel gauge to transfer dimensions accurately. Always mark cuts with a pencil before sawing—this prevents costly mistakes. For cutting, practice with hand saws first before moving to power tools like jigsaws. Safety goggles and sharp blades ensure clean edges.
- Drill pilot holes before screwing to avoid splintering.
- Test glue joints on scrap wood before final assembly.
- Carve details using a rotary tool for intricate designs.
“Accuracy in joinery turns rough blocks into cherished toys,” writes Chris West in Turning Vintage Toys. This advice highlights how tight joints define durable playthings. Beginners often rush, but slowing down builds skills like those of professional custom toy manufacturers.
When attaching small parts, use clamps to hold pieces while glue dries. For rounded edges, sand in circular motions with 220-grit paper. Books like Small Woodturning Projects by Bonnie Klein offer 12 beginner-friendly projects, while Mark Baker’s 30-Minute Woodturning includes quick techniques adaptable to toy-making. Always maintain tools—wipe blades after use and store in a dry area.
Mistakes happen. If a cut goes wrong, use wood filler or reshape the piece into a new design. Remember: even imperfections add character to personalized wooden toys. Practice these methods, and soon you’ll master the same skills that custom toy manufacturers use to create timeless playthings.
Adding Moving Parts and Mechanical Elements
Transform your unique wooden toy replicas into dynamic creations by adding moving parts. A skilled can use simple mechanics to turn static models into interactive pieces. Start with basic elements and gradually build complexity, ensuring each component works smoothly.
Simple Wheel Mechanisms
Begin with wheels using wooden or metal axles. Drill aligned holes for axles to prevent wobbling. Test wheels on dowels or small metal rods. Decorative wheels can feature carved details, while functional ones need tight fits. Use glue sparingly to allow rotation.
Creating Articulated Joints
- Pivot joints let parts swing, like a hinge on a toy car door.
- Ball-and-socket joints enable multi-directional movement, ideal for arms or legs.
- Use thin dowels or brass pins for durability. Sand joints lightly for smooth motion.
Advanced Mechanical Features
Master craftsmen add gears, cranks, or cams. For example, a Tommy Gun replica might include a sliding bolt or rotating barrel using interlocking gears. Laser-cut plywood parts ensure precise fits. Study mechanical model kits to learn how gears transmit motion. Add LED lights to illuminate functional buttons or panels for realism.
Always test joints under pressure. Use clamps or jigs for accuracy. A well-designed considers both form and function, ensuring parts last through play.
Finishing and Detailing Your Wooden Creations
Finishing transforms raw wood into polished custom wooden gifts or wooden toy replicas for sale. Start by sanding surfaces with 220-grit paper for a glass-like feel. Use a router to clean edges and painter’s tape to protect areas during painting. Here’s how to perfect your project:
- Sand surfaces progressively from coarse to fine grits.
- Raise wood grain with water, then sand again for smoothness.
- Apply finishes like Waterlox or polyurethane in thin, even coats.
- Add details like pyrography designs or inlaid wood patterns.
Finish Type | Best For | Benefits |
---|---|---|
Waterlox | Outdoor toys or wooden toy replicas for sale | Durable, water-resistant, enhances wood grain |
Polyurethane | Custom wooden gifts | Glossy protective layer, easy application |
Shellac | Vintage-style projects | Quick-drying, amber tone |
Protect moving parts like axles with painter’s tape during painting. Apply three polyurethane coats for a high-gloss finish on mahogany models like the 1957 Chevy Belair. Let each coat dry fully to avoid bubbling. Popular models like the NASA Space Shuttle use this method to ensure durability while showcasing intricate details.
Final touches like hand-painted details or metal accents elevate custom wooden gifts into collectible items. Test movable parts after finishing to ensure smooth motion. Properly sealed finishes not only protect but also highlight wood’s natural beauty, making your creations ready for display or sale.
Safe and Non-Toxic Painting Methods
Bringing color to handmade wooden toys requires a balance of creativity and safety. Every stroke of paint must align with strict safety standards while enhancing the beauty of custom wooden gifts. Start by choosing materials certified for child safety.
Professional artisans rely on non-toxic paints like Golden’s GAC 200 or Minwax Wood Finish Stain. These meet ASTM F963 and EN71-3 standards, ensuring no harmful chemicals come into contact with children. A lacquer topcoat adds durability without compromising safety.
“Safety certifications are the foundation of trust in handmade toys,” states the U.S. Consumer Product Safety Commission.
Child-safe finishes require three key steps:
- Apply 3+ layers of water-based acrylic paint for even coverage
- Seal with food-grade polyurethane (check FDA compliance)
- Test edges with a 10x magnifier to ensure smoothness
Technique | Description |
---|---|
Color Washing | Apply thinned paint with a soft brush for vintage texture |
Dry Brushing | Use a dry brush to highlight wood grain patterns |
Distressing | Gentle sanding after painting to create aged patina |
Adding hand-painted details calls for precision: outline designs first using masking tape, then layer translucent colors for depth. Always finish with a clear sealant to protect artwork. These steps ensure every custom wooden gift is both beautiful and safe for little hands.
Conclusion: Sharing Your Custom Wooden Toy Replicas with the World
Your journey from crafting to sharing begins with showcasing your wooden creations. Whether you aim to become a custom toy manufacturer or sell wooden toy replicas for sale, start by documenting your work. Clear photos and detailed descriptions highlight craftsmanship, like intricate Ganesha figures from Varanasi’s artisans, known for their natural dyes and eco-friendly materials. Platforms like Etsy or a personal website let you reach global buyers seeking unique items, such as the iconic wooden cow nandi wall hanging.
Building a brand means more than just having a product. Highlight durability and safety in listings, emphasizing materials like Sal or Seesham wood. Pricing must balance material costs with market demand—research shows targeting specific groups, like collectors or museums, can open unexpected opportunities. For instance, one entrepreneur discovered maritime museums valued hand-carved ship replicas over typical toy buyers.
Legal steps matter too. Ensure listings include safety certifications and age guidelines. Insurance and disclaimers protect your business, especially when selling to global markets. Even small-scale sellers benefit from clear terms, mirroring how brands like Drunk Elephant built trust through transparency.
Sharing doesn’t always mean selling. Donate toys to schools or workshops to teach others. Every creation preserves tradition while inspiring new makers. Whether you scale into a custom toy manufacturer or keep it personal, your wooden replicas connect timeless artistry with modern markets. Let your tools and techniques tell a story that resonates with eco-conscious buyers and collectors alike.
FAQ
What types of custom wooden toy replicas can I create?
Where can I find materials for making personalized wooden toys?
Are there specific tools I need to get started in wooden toymaking?
How can I ensure the wood I choose is safe for children?
What are good techniques for designing my wooden toy replicas?
How do I finish my wooden toys professionally?
Can I incorporate moving parts into my wooden toys?
Are there resources available for selling my handmade wooden toys?
What’s the most rewarding aspect of creating custom wooden toys?
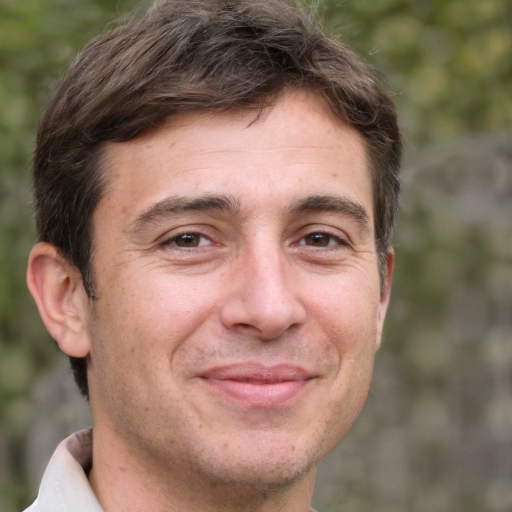
Oliver Bennett is a passionate craft writer and eco-conscious woodworker, specializing in rustic décor, sustainable projects, and handmade wooden toys. He shares practical tips and timeless inspiration for homes that value creativity and natural materials.