Did you know that the Joinery project has brought 81 traditional wood joints to life through animated 3D models? These digital recreations, crafted using Autodesk Fusion 360, reveal how Japanese joinery techniques have mastered the art of interlocking wood without nails or screws. Traditional Japanese joinery uses nothing but precisely cut angles and grooves to create structures so durable they’ve withstood earthquakes and centuries of use.
From temples to modern homes, these traditional Japanese woodworking joints rely on friction and geometry to hold buildings together. The H Carpenter YouTube channel has racked up millions of views showcasing this craft, with 193 dedicated videos explaining how these joints work. By using zero metal fasteners, these methods avoid rust damage while allowing structures to flex during earthquakes—and even be taken apart like LEGO pieces for relocation or repair. This guide explores how ancient techniques continue inspiring both artisans and engineers today.
The Art and History of Japanese Joinery
Japanese carpentry methods have shaped architectural and artistic traditions for centuries. Rooted in necessity and nature, these techniques emerged as solutions to Japan’s seismic challenges and abundant forests. Over time, they evolved into precise, elegant systems that define cultural identity.
Origins of Japanese Woodworking Traditions
Early Japanese joinery arose from practical needs. The Edo period (1603–1868) saw refined techniques applied to temples and homes. Wood’s flexibility and Japan’s forest-rich landscape—66% of land covered by trees—fueled innovation. Earthquakes demanded strong yet flexible structures. Joints like the tsugite and shiguchi were tested over centuries, proving their resilience.
Cultural Significance in Japanese Architecture
Joinery in japanese woodworking became more than function—it became art. The Katsura Imperial Villa, built in the 17th century, uses over 50 joinery techniques. Its Cryptomeria cedar structures, crafted without nails, blend indoor and outdoor spaces. Books like Wood Joints In Classical Japanese Architecture by Torashichi Sumiyoshi and Gento Matsui detail these innovations. Modern books like The Art Of Japanese Joinery by Kiyosi Seike highlight their timeless beauty.
The Philosophy Behind Japanese Joinery
Philosophy guides every cut. Harmony with nature, simplicity, and respect for materials define these methods. Zen ideals of “wabi-sabi”—finding beauty in imperfection—shape designs. Precision and patience are key, turning wood into enduring art. These principles ensure joints last centuries, embodying balance between form and function.
Understanding the Fundamentals of Japanese Joinery Techniques
Japanese joinery techniques rely on precision and harmony with wood’s natural properties. At their core, these methods avoid nails or adhesives, using interlocking joints that endure centuries. Wood selection is critical: craftspeople choose species like Japanese cypress or hinoki, considering grain direction and moisture content to prevent warping.
Key principles include allowing for wood movement and distributing stress evenly. Joints like the hozo—hidden grooves—hide structural elements, blending form and function. The tsugite (end joint) and shiguchi (corner joint) exemplify how these techniques balance strength and aesthetics.
Joint Type | Japanese Name | Purpose |
---|---|---|
Mortise and Tenon | Tsugite | Connecting beams in frameworks |
Dovetail | Kastumi-tsugi | Joining drawer fronts and boxes |
Corner Joint | Shiguchi | Securing corners in furniture and structures |
Mastering these techniques demands sharp tools like kanna planes and ryoba saws. Books like Hideo Sato’s Complete Japanese Joinery and online resources like Chris Hall’s The Carpentry Way blog offer step-by-step guidance. Beginners start with basic joints, gradually advancing to complex forms like the kanawa-tsugi scarf joint.
Essential Tools for Traditional Japanese Woodworking
Mastering Japanese joinery tools starts with understanding their unique design. Unlike Western tools, these are pulled to cut, offering precision vital for learning japanese joinery. Craftsmen rely on specialized instruments to shape joints like the kanawa tsugi, requiring exactness in every tool.
Japanese Saws and Their Unique Properties
Pull-cut saws dominate Japanese woodworking. The Ryoba features double edges for cross and rip cuts. The Dozuki, a fine-tooted backsaw, excels in precision joinery. Kataba saws, with single edges, cut smoothly on the pull. Each saw’s tooth pattern matches its task, from delicate dovetails to heavy timber work.
Chisels and Marking Tools
- Oiire Nomi: General chisels in Mentori or Kaku-uchi profiles for mortising.
- Ichou-gata Nomi: Fishtail chisels carve half-blind dovetails with precision.
- Shinogi Nomi: Triangle-section chisels for mortise walls.
Top brands like Kunikei and Kikuhiromaru forge blades with Hagane steel for longevity. Handles of Gumi or boxwood ensure grip stability during repetitive use.
Specialized Equipment
Handplanes like the Dozuki-kanna smooth surfaces, while hammers like Genno strike chisels. Jigs align joints perfectly, reducing guesswork. A traditional toolbox includes sliding lids and dado joints for compact storage of essential japanese joinery tools.
Setting Up Your Workspace
Workbenches should allow tool access and joint assembly. Lighting must highlight grain patterns. Organize tools by use—chisels near mortising areas, saws near cutting zones. A clutter-free space prioritizes safety and precision, key for learning japanese joinery.
The Five Basic Japanese Joinery Methods
Traditional Japanese woodworking joints form the foundation of this timeless craft. These five methods balance structural integrity with artistic precision, ensuring pieces endure for generations. Each joint type addresses specific challenges, from extending timber lengths to creating invisible connections.
- Tsugite (End Joints): These connect wood pieces end-to-end, crucial for lengthening timber in regions with limited long logs. Used in beams and posts, they rely on precise saw cuts and chisel work to align edges seamlessly.
- Shiguchi (Corner Joints): Form 90-degree angles in furniture and building frames. Their angled cuts resist twisting, making them vital for stable corners in shrines and cabinets.
- Katsumi-tsugi (Dovetail Joints): Distinctive interlocking pins and tails create strong, nearly invisible bonds. Osaka Castle’s Otemon Gate uses mountain-shaped dovetails that lock without nails, showcasing their structural elegance.
- Mechigai-tsugi (Dadoed Joints): Perpendicular connections for beams and frames. The stepped gooseneck scarf joint (Mechigai Koshiire Kama Tsugi) uses stub tenons to resist twisting in heavy load areas.
- Kawai-tsugite (Splice Joints): Nearly invisible when viewed from certain angles, these joints hide their mechanics. The kanawa tsugi uses story sticks for precise end-to end splicing, while shiribasami uses hidden pins for clean aesthetics.
These methods require mastery of Japanese tools like pull saws and laminated steel chisels. Techniques like the konozu zashi—a hardwood double plug joint—showcase how material selection enhances strength. Each joint reflects the philosophy of japanese wood joinery’s harmony between form and function, ensuring beauty without sacrificing durability.
Japanese Joinery for Beginners: Where to Start
Embarking on japanese joinery for beginners can feel overwhelming, but starting small builds confidence. Focus on mastering basic cuts and simple joints first. Learning japanese joinery requires patience—think of each project as a step toward mastery.
Begin with softwoods like cedar or pine, which are forgiving for mistakes. Avoid dense hardwoods until your skills develop. Essential tools include a pull saw, chisel, and marking gauge. Even basic versions of these tools suffice for early projects.
“The first cut is never perfect—but every cut teaches,” says Jin Izuhara in Japanese Woodworking: A Beginner’s Guide.
- Start with lap joints or mortise-and-tenon basics before advancing.
- Practice marking lines with a kakizuke knife for precision.
- Use scrap wood to drill and chisel test mortises.
Wood Type | Best For | Why It Works |
---|---|---|
Cedar | Practice joints | Soft grain reduces effort, ideal for learning saw control |
Hinoki | Decorative projects | Natural oils resist rot, easy to carve |
White Pine | Tool setup tests | Smooth texture shows chisel skill progression |
Beginners often overlook tool maintenance. Sharpen chisels regularly—dull blades cause frustration. The book Woodworking Joinery by Hand by Toyohisa Sugita offers step-by-step chisel setup guides. Start with small projects like a tool box lid using simple dovetail joints. Track progress with a practice log: date, joint type, and notes on what to improve next. Remember, every master once started where you are.
Step-by-Step Japanese Joinery Tutorial: Creating a Simple Mortise and Tenon Joint
Mastering the mortise and tenon joint is foundational to japanese joinery techniques. This japanese joinery tutorial breaks the process into clear stages using traditional methods. Begin by selecting straight-grained wood with 8-12% moisture content. Tools needed include a marking gauge, backsaw, chisel, and doweling jig.
“Precision over speed is key to achieving a perfect fit,” advise master carpenters.
Preparing Your Materials
- Select straight-grained hardwood like oak or cherry
- Sharpen chisels to a 25° bevel using a whetstone
- Secure wood in a bench vise with soft jaws to prevent dents
Marking and Layout Techniques
Use a marking gauge to scribe tenon shoulders at 3/8″ thickness. Mortise depth must be 1/16″ deeper than tenon length. Apply a carpenter’s pencil to outline the tenon shoulder lines.
Joint Part | Dimension |
---|---|
Tenon length | 1-1.5 inches |
Shoulder width | 7/32″ (5/16″ for thicker joints) |
Mortise depth | +1/16″ over tenon length |
Cutting and Shaping the Joint
- Cut tenon cheeks with a dozuki backsaw along marked lines
- Drill pilot holes using a doweling jig for mortise alignment
- Pare walls smooth with a 1″ bench chisel, working from both sides
Assembly and Finishing
Apply wood glue to all mating surfaces. Assemble joints and clamp for 2 hours. Test fit by gently tapping with a rawhide mallet. Sand final assembly with 220-grit paper for a seamless finish.
Advanced Japanese Wood Joinery Techniques
Japanese carpentry methods hide masterpieces in their most intricate joints. Beyond basics like mortise and tenon, these advanced techniques showcase centuries of innovation. The traditional japanese woodworking joints here push precision to its limits, blending strength with elegance.
Kanawa Tsugi (Mortised Dovetail Joint)
This joint interlocks beams with dovetail shapes cut into both ends. Used in roof frameworks, it resists both tension and compression. Miyadaiku carpenters spend over a decade perfecting cuts so tight they need no nails or glue. The overlapping tails and pins distribute weight evenly, seen in structures like the Horyu-ji Pagoda.
Shiho-Kama Tsugi (Four-Way Gooseneck Joint)
At beam intersections, this four-sided joint curves like a goose’s neck. Its angles redirect stress across all connected members. Modern architects like Shigeru Ban revived it in the Tamedia Office Building, using prefabricated wood parts to mimic traditional precision. Each angle requires meticulous measurement—slips here mean starting over.
Yatoi-Mizo (Hidden Dovetail Joint)
Used in chests and cabinets, this dovetail hides its joinery entirely. The visible surface remains smooth, while the interlocking tails secure the structure. Hinoki wood’s elasticity lets it flex during earthquakes without breaking, a trait vital in regions prone to tremors.
These joints demand patience. Apprentices spend years practicing cuts on scrap wood. The payoff? Structures like the Yusuhara Wooden Bridge Museum prove their timelessness—its laminated timbers use updated versions of these techniques. Even today, these methods teach: precision and patience build what lasts.
Modern Applications of Traditional Japanese Carpentry Methods
Traditional japanese carpentry methods are finding new life in contemporary design. Architects like Shigeru Ban blend joinery in japanese woodworking with modern materials, creating earthquake-resistant structures using techniques like the kama-tsugi. These methods adapt ancient precision to today’s needs.
Traditional Technique | Modern Application |
---|---|
Kanawa-tsugi (mortised joint) | Modular furniture systems |
Kama-tsugi (gooseneck joint) | Earthquake-resistant building frameworks |
Yatoi-mizo (hidden dovetail) | Contemporary cabinetry and decor |
Modern tools like CNC machines and CAD software amplify precision in crafting traditional joints. For example, sugi and hinoki wood—still prized for their durability—are now paired with parametric design to create eco-friendly buildings. The 10x variety of traditional joints compared to modern prefabricated systems offers unmatched flexibility.
Custom tools from masters like Eiichi Yokota inspire modern craftsmen, merging hand-cut joinery in japanese woodworking with digital workflows. Sustainable practices, such as using non-toxic adhesives and reclaimed wood, align with global eco-conscious trends.
From Tokyo to New York, designers blend japanese carpentry methods with global aesthetics. These techniques prove timeless, proving that centuries-old ingenuity still shapes modern creativity.
Common Challenges in Learning Japanese Joinery and How to Overcome Them
Learning Japanese joinery demands patience and adaptability. Whether you’re a learning japanese joinery enthusiast or a japanese joinery for beginners student, these tips help navigate common hurdles.
Working Without Nails or Fasteners
Traditional joinery relies on wood-to wood connections held by tension and friction. A 17th-century temple still stands today using this method, proving its strength. Start small: practice joints with scrap wood to grasp how fit and grain direction create stability. Use online tutorials to study how master carpentersers calculate tolerances.
Achieving Precision in Hand-Cuts
Precision comes from practice, not talent. Follow these tips:
- Sharpen tools daily—dull blades cause sloppy cuts
- Use kanna planes for smooth surfaces before fitting joints
- Practice sawing along the wood grain to prevent splintering
Joinery schools like theSakaijo Woodwork Instituteoffer drills to build muscle memory.
Adapting to Japanese Measurement Systems
Japanese Unit | Inches | Centimeters |
---|---|---|
Shaku | 11.93″ | 30.3cm |
Sun | 1.19″ | 3.03cm |
Other Resources | Conversion charts online | Apps like ShakuCalc simplify metric conversions |
Beginners can use rulers marked in both systems until they grow comfortable. Many japanese joinery for beginners courses provide dual-unit templates for projects.
Physical and Mental Mastery
Handling 50-100lb wood requires core strength. Start with lightweight cedar for practice. Mental focus improves with daily 15-minute carving sessions. Online forums like Woodworkers of Japan offer troubleshooting tips from community members.
Language and Resource Access
Online platforms like JapanWoodCraft offer English guides. Use translation apps for Japanese tool manuals. Attend virtual workshops with instructors who speak English to bridge cultural gaps.
Resources for Deepening Your Understanding of Japanese Woodworking Joints
Explore trusted resources to master japanese wood joinery and source authentic japanese joinery tools. Whether you’re a beginner or an enthusiast, these options provide pathways to hands-on learning and inspiration.
- Books: Start with Japanese Wood Joining by Toshio Odate, a classic guide detailing techniques and tool usage. For deeper cultural context, Japanese Joinery: A Complete Guide by Teruhiro Yonezawa explores historical and modern applications.
- Online Learning: Platforms like Udemy and Craftsy offer courses with video demos of mortise-and-tenon cuts or kinegata-chigiri-tsugi patterns. Search for instructors specializing in Japanese hand tool techniques.
- Workshops: The Japan Folk Crafts Museum hosts seasonal classes. Overseas, North Bennet Street School in Boston teaches traditional Japanese joinery with modern project applications.
- Tool Retailers: Brands like Marples and Lee Valley Tools stock quality chisels and saws. Look for high-carbon steel blades for precision cuts.
- Online Communities: Join the Japanese Woodworking Enthusiasts forum on Reddit or follow Instagram accounts like @japanesewoodcraft for project showcases and troubleshooting tips.
“The essence of japanese wood joinery lies in harmony between material and maker.” — Toshio Odate, woodworking pioneer
Archival projects like the Yusuhara Wooden Bridge Museum, designed by Kengo Kuma, offer real-world examples of interlocking joints. For tool maintenance, refer to Marples’s care guides to keep chisels sharp and saw blades aligned. Whether through hands-on classes or digital tutorials, these resources turn curiosity into craftsmanship.
Conclusion: Embracing the Timeless Craft of Japanese Joinery
Japanese joinery techniques embody centuries of wisdom, merging practicality with artistry in every interlocking joint. From the Golden Pavilion’s intricate Suitsuki-sashi-shikuchi joints to the Tokyo Skytree’s modern adaptations, these methods prove their enduring relevance. Traditional japanese woodworking joints like Kakushi-arigata-kumi-tsugi, with their hidden dovetails, showcase precision that transcends time. Hand tools like chisels and saws remain vital, ensuring authenticity in every cut.
This craft isn’t just about building—it’s a philosophy. It teaches respect for materials, patience in process, and the beauty of functional simplicity. Modern woodworkers worldwide now adapt these methods, proving their timeless value beyond cultural boundaries. Whether crafting a small project or large-scale structures, these techniques offer a connection to history while inspiring innovation.
Learning Japanese joinery begins with curiosity. Start with basic mortise-and-tenon joints, then explore complex forms. Each step builds skill and appreciation for the balance between human touch and natural materials. Resources like detailed guides and workshops make mastering these methods accessible even to beginners. The tools and principles endure, waiting to be rediscovered by those eager to honor tradition while shaping new creations.
Every joint tells a story of patience and precision. By embracing these techniques, woodworkers join a legacy that spans centuries, turning wood into enduring art. Whether restoring historic buildings or designing modern furniture, Japanese joinery invites continuous learning—a testament to craftsmanship that bridges past and future.
FAQ
What are Japanese joinery techniques and why are they important?
How did Japanese joinery techniques evolve historically?
What are some common joints used in Japanese woodworking?
What tools are essential for beginners learning Japanese joinery?
Can anyone learn Japanese joinery, or is it only for experienced woodworkers?
What challenges might beginners face in learning Japanese joinery?
Are there modern applications for traditional Japanese joinery techniques?
What resources are available for further learning about Japanese woodworking?
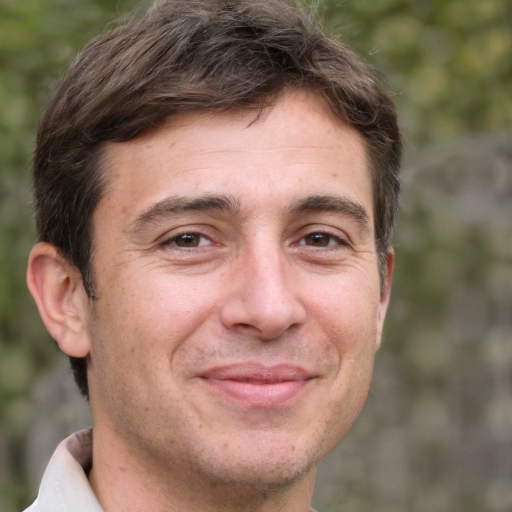
Oliver Bennett is a passionate craft writer and eco-conscious woodworker, specializing in rustic décor, sustainable projects, and handmade wooden toys. He shares practical tips and timeless inspiration for homes that value creativity and natural materials.