Did you know that improperly restoring a vintage wooden train can reduce its value by up to 40%? For collectors, the debate over vintage wooden train repair methods splits enthusiasts: some prioritize preserving original wear, while others embrace careful restoration. Proper antique train restoration requires balancing these approaches to avoid damaging historical authenticity.
BRIO trains, for example, demand precise materials like beechwood replacements and Tamiya TS-10 French Blue lacquer to match original finishes. Techniques like steaming dents with an iron or removing stickers with Goo Gone ensure authenticity. Even minor steps—like using 400-grit sandpaper for edges—matter when recreating that sought-after “aged but cared for” look.
Every restoration starts with disassembly, where WD-40 loosens rusted bolts and naval jelly tackles corrosion. Documenting each step with photos and notes helps track progress, whether repairing wheels with genuine BRIO parts or repainting with Krylon spray enamels. Done right, these methods can even boost a toy’s value by enhancing condition without erasing its heritage.
Understanding the Value and History of Vintage Wooden Trains
Wooden trains from the mid-20th century carry more than nostalgia. Their history shapes their value and guides proper vintage wooden train repair. From the 1940s to the 1970s, these toys were crafted with hardwoods like beech and pine, embodying craftsmanship that defines their legacy.
The Golden Era of Wooden Train Manufacturing
BRIO, Lionel, and Skaneateles-Playskool dominated this era. Early BRIO trains (1950s–1970s) used wooden wheels and metal axles. Key milestones include:
- 1957: BRIO launched its first wooden track systems with hand-carved details.
- 1980s: Shift to plastic wheels and Asian production began, altering collectibility.
- 2003: Skaneateles-Playskool’s closure ended an era of American-made wooden trains.
Identifying Valuable Collections and Rare Models
Rare models like BRIO’s 1970s tipping coal wagons or Lionel’s early electric sets demand attention. Key identifiers include:
- Original packaging and unaltered components.
- Marks like “Made in Sweden” for pre-1990s BRIO trains.
- Pre-1980s models with all-wooden axles and no plastic parts.
Why Preservation Matters: Cultural and Financial Value
Preserving wooden trains honors their role in toy history. Proper classic locomotive refurbishment maintains cultural ties to craftsmanship. Financially, pre-1980s BRIO sets with original finishes can fetch hundreds. For instance, unrestored 1960s Lionel trains retain 90% of their value when preserved authentically. Collectors prioritize pieces made before material shifts to plastic, ensuring their historical significance endures.
Essential Tools and Materials for Vintage Wooden Train Repair
Successful vintage toy train maintenance starts with the right tools. Basic kits include small screwdrivers like #1 and #2 Phillips heads and triangle drivers for disassembling intricate parts. Safety screwdrivers with non-stick coatings prevent stripping delicate screws. For precision work, needle-nose pliers and hemostats handle tiny components, while sandpaper (220-400 grit) smooths wood surfaces without damaging finishes.
- Cleaning: Cotton swabs and isopropyl alcohol clean crevices. Microfiber cloths avoid scratching painted surfaces.
- Repair: Wood glue bonds joints; epoxy fills cracks. Exact-O knives cut replacement wood pieces to match original beech or pine.
- Finishing: Specialty paints like Rust-Oleum Lacquer and Tamiya model paints match historic colors. Plastic-safe lubricants protect moving parts from rust.
Brand | Product | Use |
---|---|---|
Rust-Oleum | Lacquer Spray (Black/White) | Base coats for locomotives |
Tamiya | TS-10 French Blue | Classic color for vintage designs |
Tamiya | TS-35 Park Green/Yellow | Period-accurate finishes |
Storage solutions like a $11.49 Home Depot parts box organize screws and small pieces. Safety gear includes dust masks for sanding and reading glasses with magnification for detailed work. Even basic craft tweezers work for budget repairs, though high-quality tools like tiny socket sets prevent stripped fasteners. Always test paints and adhesives on scrap wood first to ensure compatibility with wooden railroad model repair needs.
Assessing Your Vintage Wooden Train’s Condition
Before starting antique train restoration, thoroughly inspect every part of your model. Begin by checking paint for peeling or cracks. Look for wood splits, warping, or water damage. Test wheels for smooth rotation and inspect metal parts for rust. Loose screws or stripped bolts signal past mishandling. Note missing components like wheels or track pieces. Some models, like the BRIO Blue Steam Engine, demand extra care to retain value.
Common Damage Patterns in Antique Wooden Trains
- Paint: Chips, fading, or flaking surfaces
- Wood: Cracks along joints, insect damage, or moisture stains
- Hardware: Bent axles, rusted couplers, or stripped screw holes
- Plastic: Warping from heat or brittle parts
- Electrical: Cracked wires or frayed connectors
Creating a Detailed Restoration Plan
Document every flaw with photos. Research original specs using manufacturer catalogs or online archives. Prioritize repairs: stabilize structural damage first, then cosmetic fixes. Budget time and costs—old-fashioned train refurbishing can take weeks. List tools and materials needed, like wood glue or non-water-based finishes. Avoid WD-40 on plastic gears, as it causes deterioration.
When to Restore vs. Preserve
Rare or historically significant trains (like pre-1950s Märklin models) may need preservation to retain value. If damage is severe but the model is common, full restoration is safer. Ask: Will this train be displayed or used? Play-focused models need functional repairs, while display pieces prioritize original aesthetics. Never mix restoration methods mid-project—stick to one approach.
Vintage Wooden Train Repair: Step-by-Step Techniques
Restoring a vintage wooden train requires careful hands-on work. Start by cleaning surfaces gently. Test any cleaner first on a hidden area. Use a damp cloth for light stains and a soft toothbrush to reach details. Avoid 409 or Windex—they can strip finishes. For tougher marks, 3M Light Duty Compound (#051144-05935 works well. Always rinse with water and dry completely before moving forward.
Fixing dents needs patience. Apply a drop of water to the dent, cover with a cloth, then steam with an iron on low heat. This may reshape warped wood but requires caution to avoid burns. Skip this method if the piece feels unstable. After drying, sand lightly with 220 grit paper for a smooth finish.
Structural repairs begin by gluing cracks with wood glue. Clamp pieces firmly and wipe excess glue with a cloth. For missing parts, use matching wood scraps. Sand edges smooth once dry. Axles and wheels need careful attention. Clean bearings with mineral spirits, then lubricate with light oil. Replace stripped axles using brass rod cut to original size.
Metals parts like smokestacks or wheels deserve special care. Use vinegar and baking soda paste to remove rust. Buff with steel wool for shine. Reattach loose hardware using threadlock compound. When replacing missing parts, reference period-correct designs. The GREENBERG’S LIONEL POSTWAR REPAIR BOOK offers exact factory repair methods for 1945-1969 models. It’s available on eBay with clear instructions and diagrams.
Take your time. Every step matters to keep your train’s authenticity. Small repairs add up to a fully restored piece of history. Patience and precision ensure a treasured retro wooden locomotive restoration.
Authentic Finishing and Painting Methods
Finishing touches are the final step to revive your wooden train’s original charm. Whether restoring a vintage steam engine repair or an antique railway car renovation, attention to detail ensures authenticity. Start by researching historical references—like Lionel or American Flyer catalogs—to match colors and patterns from the train’s era.
Researching Original Color Schemes and Designs
Historical accuracy starts with research. Compare your train to period photos or manufacturer catalogs. Use color-matching tools to replicate faded finishes. For example, Lionel’s 1950s models often featured deep reds and blues, while brass details were common on early 20th-century replicas.
Traditional Paint Mixing and Application
- Prepare surfaces by sanding with 220-400 grit paper.
- Clean wood with isopropyl alcohol to remove residue.
- Apply thin acrylic layers using brushes or airbrushes. Let each coat dry 24 hours.
Weathering adds realism: use rust red washes for metal parts and dry-brush techniques to highlight grooves. Test colors on scrap wood first.
Clear Coating and Protection Techniques
Protect finishes with Minwax Polyshades stains followed by three clear coats of polyurethane. Sand lightly between coats with 400-grit paper. Let cure fully for 30 days to avoid solvent damage. Use beeswax polish to enhance wood grain without obscuring details.
“A rushed finish ruins months of work. Let each layer dry properly.”
Patience ensures your restored train looks as it did when first built—ready to inspire future generations.
Restoring Mechanical Elements in Classic Locomotive Models
Classic locomotive refurbishment requires careful attention to moving parts. Start by disassembling mechanisms gently to avoid breaking fragile gears or springs. Use mineral spirits to clean grease from motors and wheels, then dry thoroughly. Lubricate bearings with sewing machine oil and test parts for smooth movement. For wooden railroad model repair, replace worn gears using materials like 108LB Model Glue for secure bonds.
- Use cotton swabs to clean tight spaces in motors and axles.
- Lubricate joints with Bachmann EZ-Lube Grease for long-lasting motion.
- Test restored parts with a Superior power pack to check alignment and speed.
A comparison of repair vs. restoration methods:
Repair | Restoration |
---|---|
Cleans and fixes broken parts | Strips and repaints to original specs |
Uses modern adhesives | Matches vintage paint formulas |
When parts are missing, recreate them using brass or plastic molds. For example, a 1918 Lionel No. 154 locomotive had its corroded wheels replaced with period-accurate designs. Always test motors after lubrication—vinegar can remove oxidation from power wheels. Remember, proper classic locomotive refurbishment balances functionality and authenticity.
Addressing Special Challenges in Antique Railway Car Renovation
Old-fashioned train refurbishing projects often uncover hidden obstacles. For example, restoring delicate features like miniature carvings or painted floral motifs requires precision. Start by testing cleaning agents on small areas to avoid damaging fragile finishes. Stabilize loose veneers with reversible adhesives, preserving original layers whenever possible.
- Use soft bristle brushes for dust removal
- Apply microfiber cloths dampened with mineral spirits
- Reinforce cracked lattice work with discreet epoxy injections
When parts are missing, sourcing authentic replacements demands creativity. The 1925 IC Caboose 9648 restoration exemplifies this: its original windows were recreated using period-correct glass patterns. For structural repairs, consult specialists like carved wood artisans for intricate details. Modern materials must mimic vintage textures—like using expanded metal grating for walkways while matching 1920s designs.
“Every repair must document material changes for authenticity,” says the Florida East Coast Railway restoration team.
Prior repairs using modern polyurethane or household paints complicate restorations. Remove acrylic-based fillers with heat guns set below 150°F to avoid warping. Reapply historically accurate stains like those used in the caboose’s $200,000 restoration, which included 18-month sanding and epoxy treatments. Always disclose restoration work when selling—include paint brand names and process details for transparency.
Remember: antique railway car renovation requires patience. Whether fixing a warped seat back or restoring brass fittings, prioritize reversible solutions to protect long-term value.
Preservation and Display of Your Restored Wooden Railroad Collection
After completing retro wooden locomotive restoration, proper care ensures your collection stays vibrant. Newly finished pieces need time—allow adhesives and finishes to cure fully before handling. The Southern Pacific shanty’s fiberglass roof repair, for instance, required patience to set before exposure to sunlight.
Store pieces in stable environments. Ideal conditions avoid extremes: 50-70°F temperatures and 40-60% humidity. Shield from UV rays—like how the Burnet Station sign’s repainting involved shielding delicate paint layers during restoration.
- Display cases with UV-protective glass are ideal for static showcases.
- Track layouts allow occasional operation, balancing activity with care.
- Rotate pieces in large collections to reduce wear on individual items.
“A restored piece’s legacy lives in how it’s cared for,” says the Hoosier Heartland Trolley Company, preserving a 1898 GE locomotive with traditional methods.
Document each item’s journey. Track vintage toy train maintenance logs, restoration steps, and photos. The Maurice Beckham dining car’s glass replacement project included detailed records of material choices to maintain authenticity.
Regular vintage toy train maintenance includes gentle dusting with soft cloths, annual condition checks, and pest-proof storage. The HHTC’s 2024 work on the David W. Peat-donated locomotive used archival-safe materials to prevent future decay.
Plan public viewings wisely. The 2021 open house showcased the restored locomotive, balancing access with protective measures. Future events should follow similar protocols to safeguard these treasures.
Conclusion: Keeping the Legacy of Vintage Wooden Trains Alive
Every vintage wooden train holds stories of craftsmanship and nostalgia. Whether a collector or hobbyist, embracing vintage toy train maintenance means keeping these pieces of history alive. Start small—a derailed wheel, a chipped caboose—using simple tools like wood glue or sandpaper. Building skills step by step turns hobbyists into confident restorers over time.
Learning from past techniques ensures authenticity. Researching original color schemes or sourcing period-accurate parts honors the train’s heritage. Even modest repairs contribute to preserving the legacy of manufacturers like Lionel or Märklin, whose designs shaped childhood memories for generations.
Joining clubs like the Train Collectors Association or online forums connects enthusiasts worldwide. Sharing tips or swapping rare parts fosters a community invested in antique train restoration. Each restored model becomes a bridge between past and present, teaching hands-on skills to younger generations.
These heirlooms aren’t just toys—they’re tangible links to an era of wooden craftsmanship. With patience and curiosity, anyone can help keep their stories rolling. The tracks of tradition are maintained one careful repair at a time.
FAQ
What is the difference between restoration and preservation of vintage wooden trains?
Which manufacturers produced the most valuable vintage wooden trains?
How can I identify potentially valuable models in my collection?
What tools do I need for repairing older wooden trains?
What are the most common types of damage found in vintage wooden trains?
When should I prioritize preservation over restoration?
How can I clean my vintage wooden train without damaging it?
What are the best practices for finishing and painting vintage wooden trains?
How can I restore complex mechanical systems in vintage locomotives?
What should I do if I encounter previous amateur repairs on my vintage train?
How should I display my restored wooden railroad models?
Why is documenting the restoration process important?
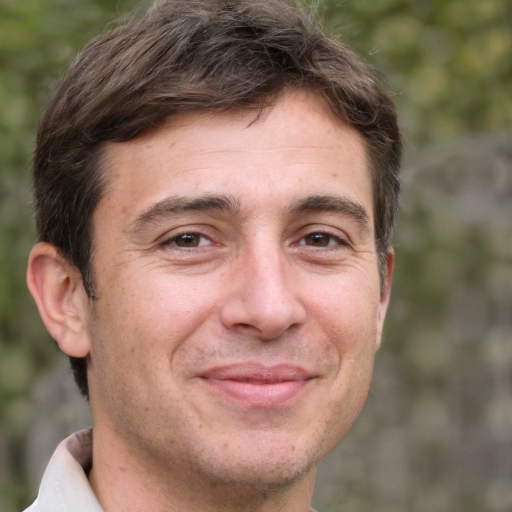
Oliver Bennett is a passionate craft writer and eco-conscious woodworker, specializing in rustic décor, sustainable projects, and handmade wooden toys. He shares practical tips and timeless inspiration for homes that value creativity and natural materials.